Wet granulation is one of the most common processes used in pharmaceutical manufacturing, especially for creating tablets. It involves turning powders into larger, more manageable granules by adding a liquid binder, which is then dried to create a uniform, compressible product. This process plays a huge role in ensuring tablet consistency, improving drug effectiveness, and making production more efficient.
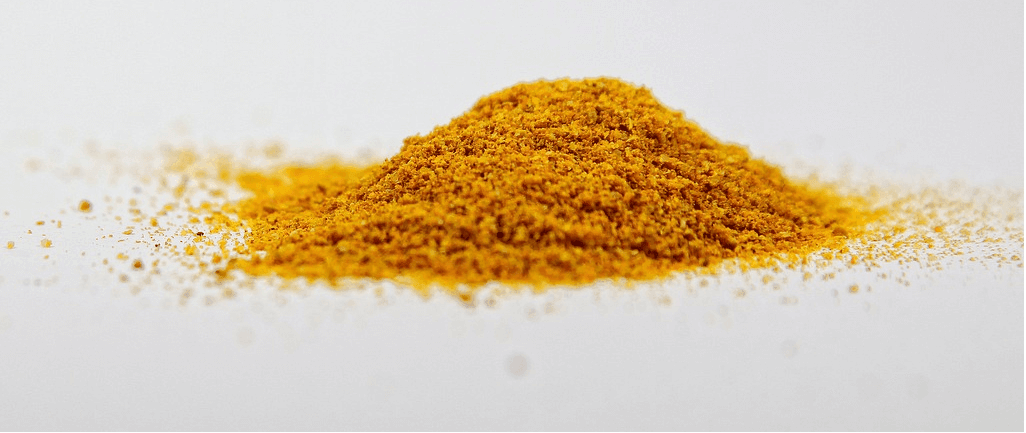
Key Benefits of Wet Granulation
1. Better Tablet Formation
Wet granulation makes powders easier to compress into tablets. The granules produced are easier to handle than loose powder, which leads to smoother tablet manufacturing. This results in better tablet quality and fewer production issues.
2. Improved Uniformity
Wet granulation helps mix active ingredients evenly with excipients. This ensures that every tablet contains the correct dose of the active ingredient, which is crucial for drugs with small doses or powerful APIs.
3. Enhanced Drug Dissolution
This process can significantly improve the dissolution of poorly soluble drugs. By creating more hydrophilic granules, wet granulation ensures that the drug dissolves faster in the body, leading to better absorption and effectiveness.
4. Reduced Dust and Segregation
Wet granulation helps minimize dust creation, which can lead to cross-contamination or safety issues. It also reduces the risk of ingredient segregation, making batch-to-batch production more consistent and reliable.
Challenges of Wet Granulation
1. More Complex and Equipment-Intensive
Wet granulation involves multiple steps like mixing, binding, granulating, and drying, which require specialized equipment. This makes the process more complicated compared to other methods, and may require more time and investment.
2. Higher Costs
The equipment needed, such as high-shear mixers and drying units, can be costly. Additionally, the process uses more energy, which increases overall production expenses.
3. Not Ideal for Moisture-Sensitive Materials
Since moisture is added during the process, wet granulation isn't suitable for drugs or materials that are sensitive to moisture or heat. For these, dry granulation or direct compression might be better alternatives.
4. Moisture Control Challenges
The drying phase is critical in wet granulation. Too much moisture can cause the granules to clump together, while too little can result in poorly formed granules. Proper moisture control is essential for achieving the right product quality.
Wet Granulation Process Simplified
Here’s how the process works in easy steps:
1. Mixing: Active ingredients and excipients are blended together to form a uniform powder.
2. Adding Binder: A liquid binder, like water or alcohol, is added to help the powder particles stick together.
3. Granulating: The mixture is agitated in a granulator, forming larger granules.
4. Drying: The wet granules are dried to remove excess moisture, usually in a fluidized bed dryer.
5. Sizing: After drying, the granules are sieved to ensure they are the right size for tablet compression.
6. Compression: Finally, the granules are compressed into tablets, which may be coated and then packaged.
Related Questions
1. What’s the difference between wet and dry granulation?
Wet granulation uses a binder liquid to form granules, while dry granulation doesn’t. Dry granulation is better for moisture-sensitive materials.
2. How does wet granulation improve tablet dissolution?
By making the granules more hydrophilic, wet granulation helps the drug dissolve more quickly in the body, improving absorption.
3. What role do binders play?
Binders are essential for holding the powder particles together, ensuring the granules stay intact and compress easily into tablets.
4. Is wet granulation suitable for all drugs?
No, wet granulation is not ideal for moisture-sensitive drugs. In such cases, dry granulation or direct compression is more appropriate.
5. How is moisture controlled in the process?
Careful control during the drying stage is essential. Too much moisture can cause clumping, and too little will result in poor granules.
Wet granulation is a powerful method in pharmaceutical manufacturing, offering key benefits like better tablet formation, improved drug dissolution, and enhanced uniformity. However, the process does come with some challenges, including its complexity and higher costs. It’s important to choose wet granulation when the benefits outweigh the challenges, particularly for drugs that require improved flow properties and dissolution.
Interested in optimizing your tablet production process?
Contact us today to explore our advanced wet granulation equipment and enjoy a five-year warranty on all machines!