Filling accuracy in capsule filling machines is crucial for ensuring the correct dosage and quality of pharmaceutical products. Various factors can influence filling accuracy, from machine wear to environmental conditions. This article explores these factors and provides practical solutions for achieving precise control over the filling process.
Filling accuracy is affected by factors such as machine condition, product consistency, environmental conditions, and operator skill. Achieving accurate control involves regular maintenance, calibration, consistent product formulation, and thorough operator training.
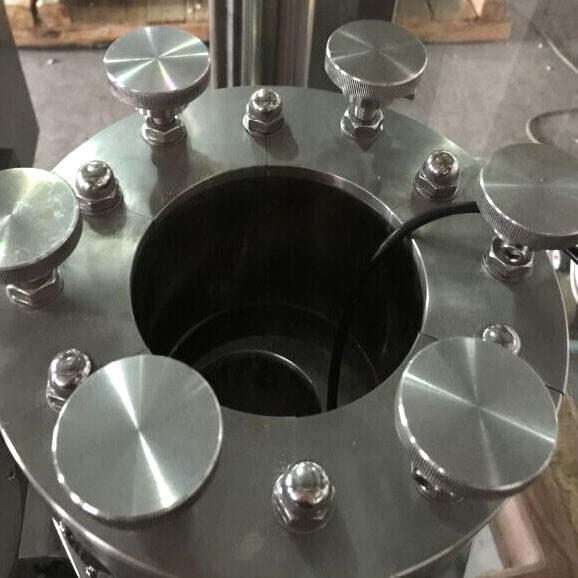
Several factors can impact the filling accuracy of capsule filling machines, making it essential to identify and address them to maintain high-quality production. Here are the key factors and how to manage them:
Machine Condition: The condition of the machine itself is a primary factor affecting filling accuracy. Wear and tear on components such as dosing discs, tamping pins, and fill shoes can lead to variations in fill weight. Regular maintenance and timely replacement of worn parts are crucial to ensure the machine operates accurately.
Product Consistency: The physical properties of the product being filled, such as particle size, flowability, and moisture content, can affect filling accuracy. Maintaining consistent product formulation and handling can minimize these variations. For instance, using properly sieved powders and controlling moisture levels can help achieve uniform filling.
Environmental Conditions: Environmental factors such as temperature, humidity, and air pressure can influence filling accuracy. These conditions can affect both the machine and the product. Implementing environmental controls in the production area, such as dehumidifiers and air conditioning, can help maintain stable conditions and improve accuracy.
Operator Skill: The skill and experience of the machine operators play a significant role in maintaining filling accuracy. Properly trained operators can quickly identify and correct issues, perform necessary adjustments, and follow standard operating procedures (SOPs) to ensure consistent performance. Ongoing training and certification programs can enhance operator competence.
Calibration and Quality Control: Regular calibration of the filling machine ensures that it continues to operate within the specified accuracy range. This involves using standard weights and measures to adjust and validate the machine’s settings. In addition, implementing robust quality control procedures, such as in-process checks and final inspections, helps detect and correct any deviations.
Having identified the factors that affect filling accuracy and the measures to control them, it is beneficial to explore related topics that provide further insights into maintaining and optimizing the filling process. The next section addresses additional considerations and solutions for ensuring consistent filling accuracy.
How to detect and verify filling accuracy? Is there an automated detection system?
Automated detection systems are available in many modern capsule filling machines. These systems use sensors and real-time data analysis to monitor and verify filling accuracy continuously, making necessary adjustments to maintain precision.
Is filling accuracy affected by the nature of the filler? How to deal with fillings of different properties?
Yes, the physical properties of the filler, such as particle size and flowability, can affect filling accuracy. Machines can be equipped with specific settings or accessories, such as different dosing disks or agitators, to handle different types of fillers effectively.
Does the filling volume adjustment process require shutdown? How to minimize downtime?
In many modern machines, adjustments can be made on-the-fly without requiring a complete shutdown. Minimizing downtime involves using machines with adjustable settings and modular components that can be quickly swapped or adjusted without halting production.
How to deal with filling errors and deviations during production? Is there an automatic adjustment function?
Many advanced capsule filling machines are equipped with automatic adjustment functions that correct filling errors in real-time. These systems detect deviations and adjust the dosing mechanism to ensure consistent fill weights, reducing the incidence of errors.
How to ensure filling accuracy over long production runs?
Maintaining filling accuracy over long production runs requires regular monitoring, periodic calibration, and consistent quality control checks. Automated systems can assist by providing real-time feedback and adjustments, ensuring stability and precision throughout the production cycle.
Filling accuracy in capsule filling machines is influenced by several factors, including machine condition, product consistency, environmental conditions, and operator skill. By addressing these factors through regular maintenance, calibration, consistent product handling, and operator training, manufacturers can achieve precise control and maintain high-quality production standards.
Are you looking to improve the filling accuracy of your capsule filling machines? Contact us today to learn more about our advanced solutions and maintenance services. Take advantage of our special offers on new equipment and calibration services. Enhance your production efficiency and product quality with our state-of-the-art technology and expert support.