The pharmaceutical industry is a high-pollution industry. In recent years, with the advancement of environmental protection policies, there are not a few pharmaceutical companies that have "slopped" on environmental issues. Due to the difficulty and high cost of pollution control. At present, how to solve the problem of economic and environmental benefits has become a topic that pharmaceutical companies have to face.
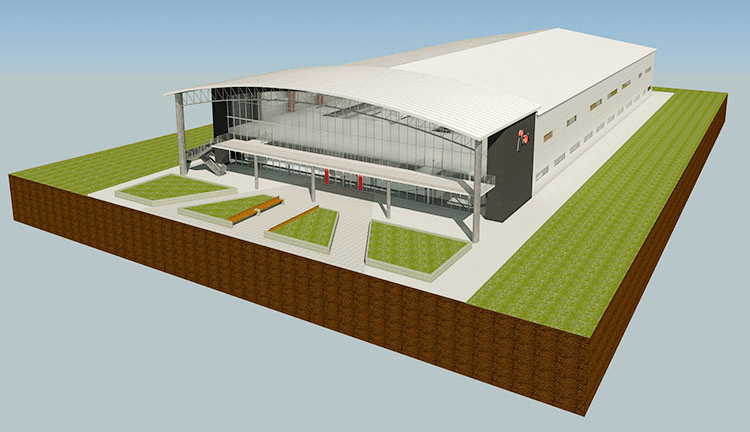
According to the industry, the original pollution development model is no longer sustainable. For pharmaceu
tical companies, the top priority is to build a dust-free purification workshop, using air purification equipment to concentrate the drug dust, volatile drug gas and other pollutants in the workshop out of the workshop. Then install purification and recovery devices in strict accordance with national standards to ensure that the gas is clean before being discharged into the atmosphere.
By constructing a dust-free medical purification workshop, pharmaceutical companies can avoid serious pollution problems on the one hand, and on the other hand, they can turn waste into treasure through recycling and even turn harm into treasure, and corporate benefits will increase accordingly. So, what aspects should be paid attention to when constructing a clean medical workshop?
Follow actual needs
Enterprises need to follow the actual needs of customers in building a clean medical workshop for customers. Purification workshops that require high cleanliness in biopharmaceuticals should use local purification measures. For example, the potting of large infusions in pharmaceutical workshops needs to be operated in a class 10,000 clean room and a local production environment of class 100. In this case, when designing the clean workshop, the manufacturer of the medical dust-free workshop does not need to achieve the 100-level purification level, but only needs to achieve the 100-level purification level.
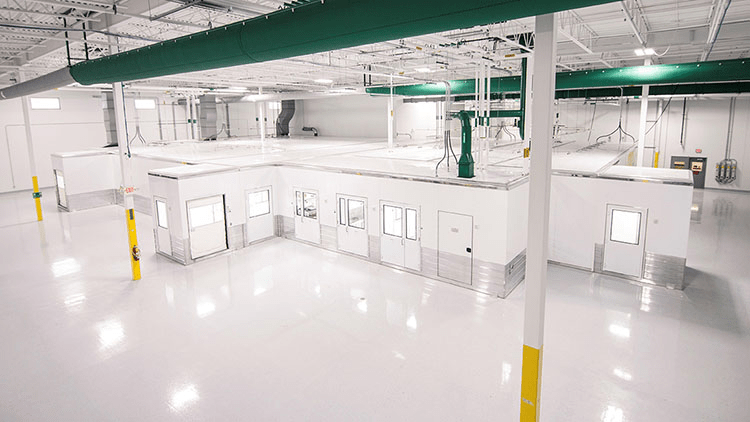
Energy issues
Energy consumption is related to the cost of the workshop. According to the industry, the design of a clean medical workshop can reduce energy consumption in a biopharmaceutical workshop. It is recommended that companies consider the size of production equipment, operation methods, maintenance, and equipment when designing a clean workshop. For factors such as cleaning and production capacity, the purification level of the clean room should be determined in accordance with the production requirements. For example, in the biopharmaceutical workshop, the requirement for the rare compound room is higher, and the 10,000-grade clean room is required, while the dense compound room has low environmental requirements , Only need to make the clean workshop reach 100,000 grade.
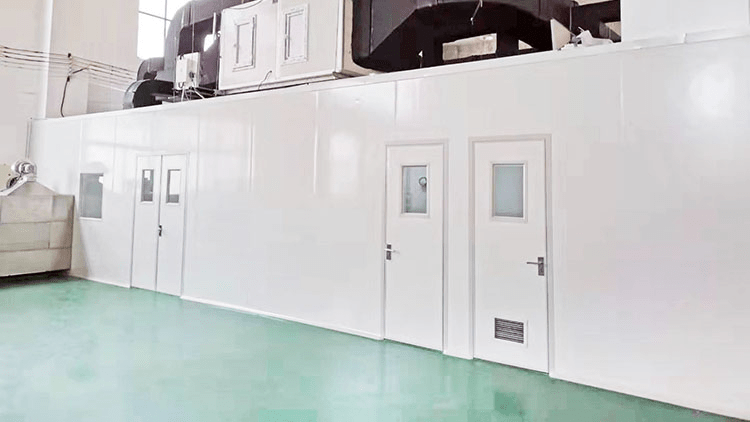
Standard aspect
According to the GMP design standard of the medical clean room, the clean room should maintain a certain positive pressure. In addition, the static pressure difference between clean areas with different air cleanliness and between the clean area and the non-clean area should not be less than 5Pa, and the static pressure difference between the clean area and the outdoor should not be less than 10Pa. Where there is a pressure difference request in the drug consumption quality management standard rules, an installation with an indicated pressure difference must be set.
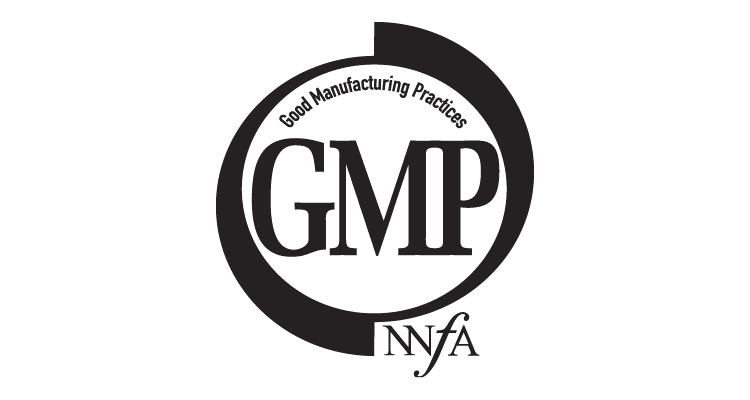
Equipment life
In addition, from the perspective of the service life of the equipment, in the clean engineering of pharmaceutical production in the medical clean room, as far as the air conditioning system is concerned, it cannot simply pursue the centralized cooling of large-capacity chillers. Otherwise, it will increase when some workshops are running. Operating costs, the system cannot be completely shut down for maintenance, it will shorten the service life of the equipment, increase the probability of failure and shutdown, affect the production of the enterprise, and increase a certain amount of maintenance costs.
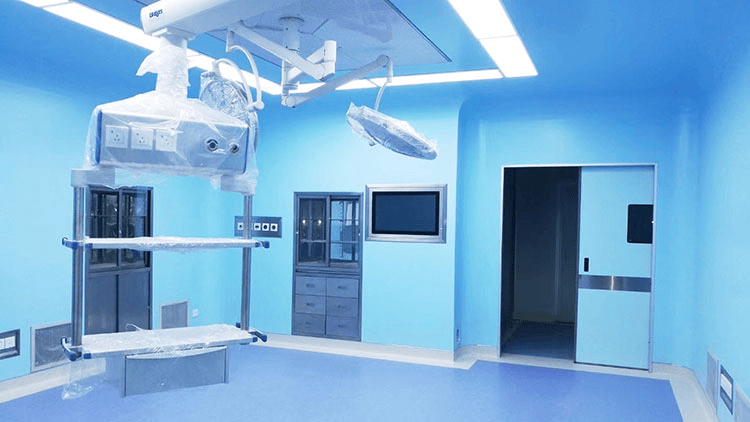