Thermoforming blisters is a method widely used in the packaging industry. This is especially true for pharmaceuticals and consumer goods. This technique involves heating plastic sheets until they become pliable, and then molding them into the desired shape with a mold. This article will provide an in-depth overview of the thermoforming process, materials and equipment.
- The Thermoforming Process
- Common Materials Used in Thermoforming Blister Packaging
- Blister Packaging Equipment and Components
- The Differences Between Thermoforming and Cold Forming Blister Pack
Thermoforming blister packing involves heating plastic sheeting and molding it to a cavity which holds the product. This cavity is then sealed using a lidding product, usually made of plastic or aluminum, to ensure the product's protection.
1. The Thermoforming process:
Thermoforming begins by heating a plastic film until it becomes soft. The heated sheet is placed over a mould and shaped into the desired shape by vacuum, pressure or mechanical means. The blister is cooled so that it retains its shape. The product is then placed inside. The blister is then sealed with a lidding film or aluminum foil to keep the product in .
2. Common Materials
- PVC (Polyvinyl Chloride): Known for its clarity and good barrier properties, PVC is widely used in blister packaging. However, it can sometimes interact with the product, so it's often coated with PVDC for added protection.
- PET (Polyethylene Terephthalate): Offers excellent clarity and strength, making it ideal for both blisters and lidding materials. PET is also recyclable, aligning with sustainability efforts.
- COP (Cyclic Olefin Copolymer): Provides high clarity and chemical resistance, making it suitable for sensitive products. However, it is more expensive and requires special processing equipment.
- Aluminum Foil: Commonly used as a lidding material, aluminum foil offers excellent barrier properties against moisture, oxygen, and light, ensuring product stability and tamper evidence.
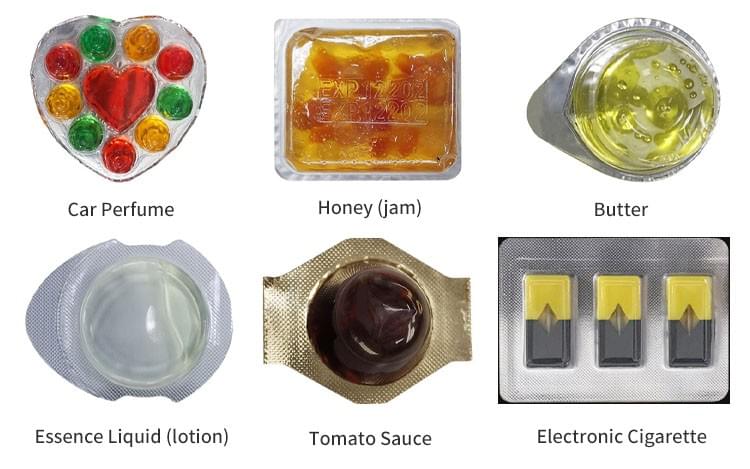
3. Blister Packaging Equipment
- Forming station: Heats up and molds plastic sheet into blisters.
- Filling station: Fills cavities with product, either manually through automated systems or by filling them automatically.
- Sealing station: Uses pressure and heat to seal the lidding to the blister, creating a tamper evident seal.
- Punching station: Cuts sealed blisters into individual packages.
- Waste Rewinder Collects leftover material and rewinds it for disposal or recycling .
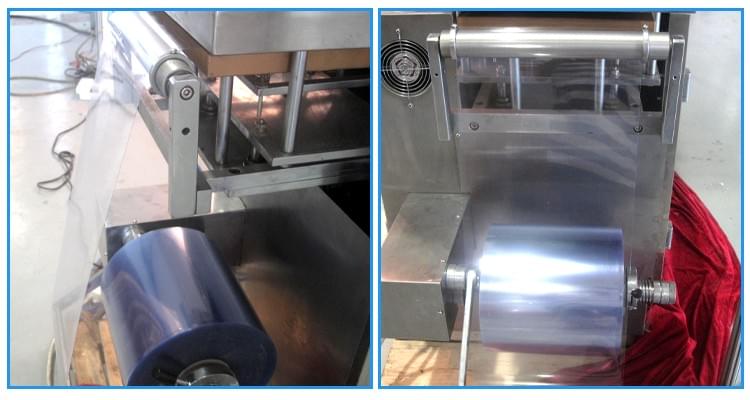
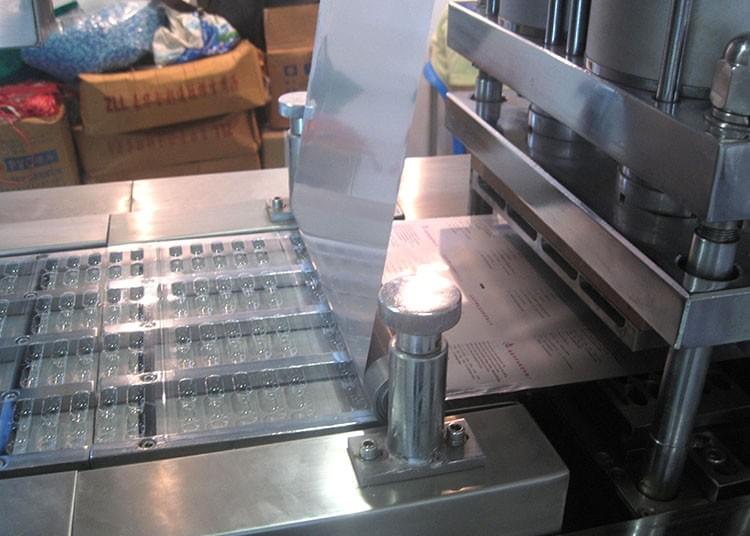
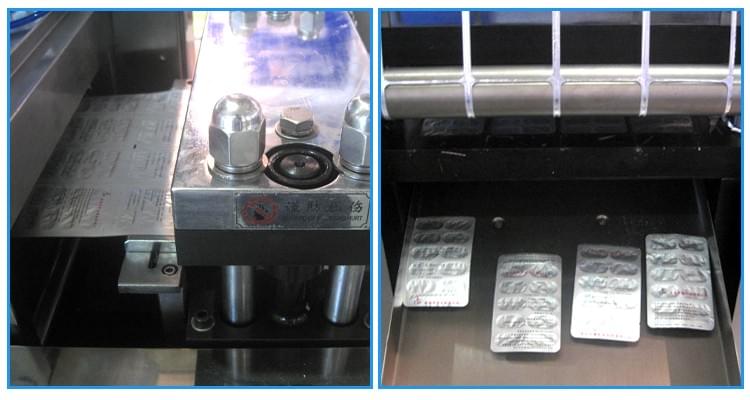
4. Differences between Thermoforming Blister Pack and Cold Forming Blister pack
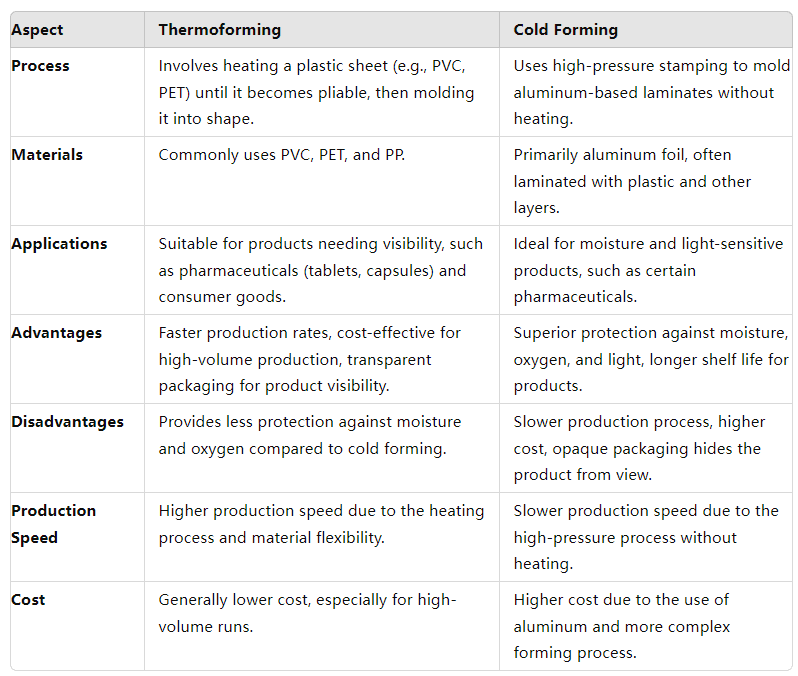
Related Topics & Answers
1.What is the advantage of thermoforming blister packing? Thermoforming offers excellent protection, clarity and tamper-evident packaging. It can be customized to fit different product shapes and sizes. This enhances consumer appeal.
2.What is the difference between thermoforming and cold forming? By using heat to mold plastics, thermoforming is suitable for products requiring a clear view. Cold forming uses aluminum, and does not require heating. It provides superior barrier properties for sensitive products.
3.What environmental considerations are there in blister packaging?
The modern blister packaging uses recyclable materials such as PET and sustainable practices to reduce environmental impact. Bioplastics and advanced recycling are key to promoting sustainability.
4.How does product load affect blister packaging?
Product load, whether automated or manual, ensures that every blister cavity is filled accurately and maintains product integrity. Automated systems are efficient and consistent, especially in high-volume production.
5.How important is quality control in blister packaging?
It's vital to ensure the precision and integrity in blister packs. This includes regular inspections of the mold dimensions, the surface finishes, and fit of the product. This ensures top-tier packaging at all times.
Thermoforming is an effective and versatile method of protecting and displaying products. Understanding the process, materials and equipment involved allows manufacturers to optimize their packaging solutions in order to meet consumer demand and industry standards.
Visit our products to learn more about thermoforming blister packaging, and to explore customized options for your products. Contact us to learn more about our specials and how we can enhance your packaging operations.