Coating pan machines are crucial for applying coatings on tablets, pills, and other products in industries such as pharmaceuticals, food, and chemicals. These machines ensure uniform application of coatings, enhancing product appearance, stability, and performance. Below, we explore the key components, working principles, and types of coating pan machines.
Key Components of a Coating Pan Machine
1. Coating Drum (Pan)
The coating drum is a rotating vessel where the tablets or products are placed. As the drum rotates, the tablets tumble, allowing for an even distribution of the coating solution. The drum is typically tilted at an angle (30-45 degrees) for efficient coating movement.
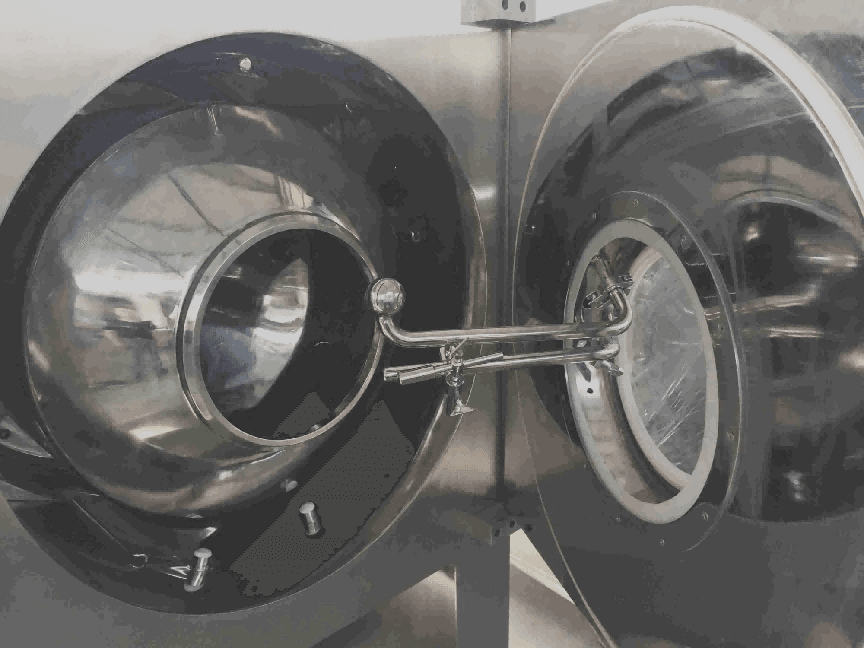
2. Spray System
The spray system applies the coating solution to the tumbling tablets. This system consists of nozzles that produce a fine mist, ensuring that the coating is evenly distributed across the surface of each tablet.
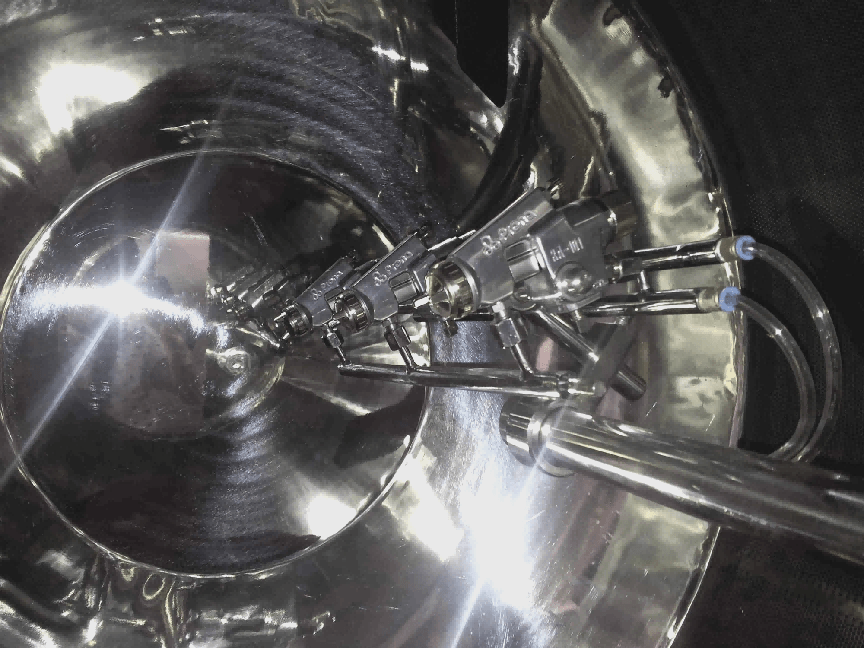
3. Air Handling System
The air handling system controls the temperature and humidity during the coating process. It ensures that the coating dries effectively, preventing the tablets from sticking together and ensuring a smooth, uniform finish.
4. Exhaust System
The exhaust system removes excess air, moisture, and solvent vapors, maintaining a clean and controlled environment inside the coating pan. This system is essential for ensuring the quality of the coating.
5. Control System
A modern control system monitors and adjusts parameters like drum speed, spray pressure, and air temperature, ensuring consistent coating quality. Advanced machines often feature PLC (Programmable Logic Controller) systems for precise control.
Working Principle of Coating Pan Machines
The coating process begins with loading tablets into the rotating drum. As the drum rotates, the tablets tumble, allowing the spray system to evenly apply the coating solution. The air handling system then helps to dry the applied coating, ensuring a smooth and uniform layer on each tablet. This process is repeated until the desired coating thickness is achieved.
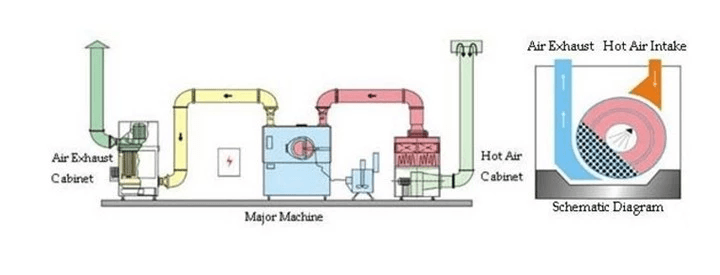
Types of Coating Pan Machines
1. Standard Coating Pan
Description: The most basic type, featuring a solid drum. The tablets tumble inside while the spray system applies the coating solution.
Applications: Suitable for small-scale or pilot production.
2. Perforated Coating Machine
Description: This machine features a perforated drum that allows for better airflow and faster drying of the coating.
Applications: Ideal for large-scale pharmaceutical production and for applying film and enteric coatings.
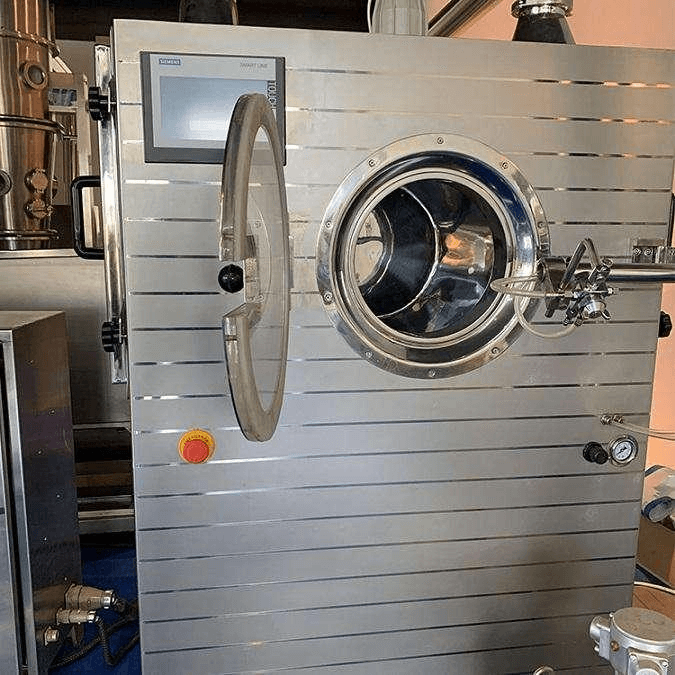
3. Fluidized Bed Coater
Description: Tablets are suspended in an air stream while the coating solution is sprayed. The constant airflow ensures even distribution and rapid drying.
Applications: Best for coating lightweight granules, powders, or pellets.
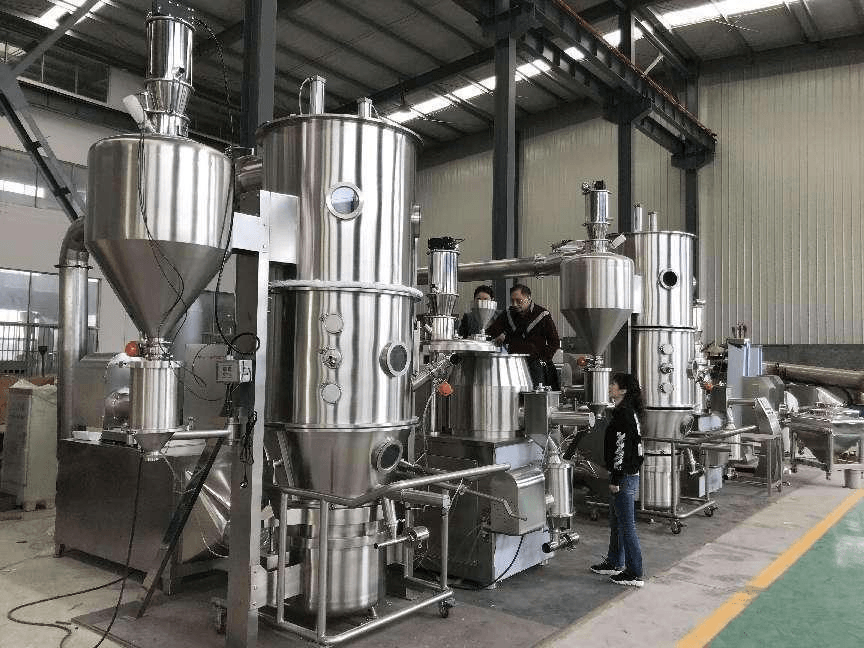
4. Continuous Coating Machine
Description: Designed for continuous production lines, this machine minimizes downtime and enhances efficiency in large-scale production environments.
Applications: Suitable for high-volume pharmaceutical manufacturing.
Common Types of Coatings
1. Film Coating
A thin polymer coating applied to tablets for protection and controlled release. Film coatings are widely used due to their efficiency and minimal effect on tablet size and weight.
2. Sugar Coating
A traditional method used to improve the appearance and taste of tablets. This multi-layer coating is applied over several stages and is typically used for large, durable tablets.
3. Enteric Coating
This coating protects the tablet from dissolving in the stomach, ensuring that the active ingredient is released in the intestine. It is essential for drugs that are sensitive to stomach acids.
Coating pan machines are essential tools for ensuring consistent, high-quality coatings on tablets and other products. Understanding the components and types of coating pan machines allows manufacturers to choose the right equipment for their specific production needs. For more information on our coating machines, visit Coating Machine.