Softgel manufacturing is a highly specialized process used to produce soft gelatin capsules, which are widely utilized in the pharmaceutical, dietary supplement, and cosmetic industries. This process involves several critical steps to ensure the quality, stability, and efficacy of the final product.
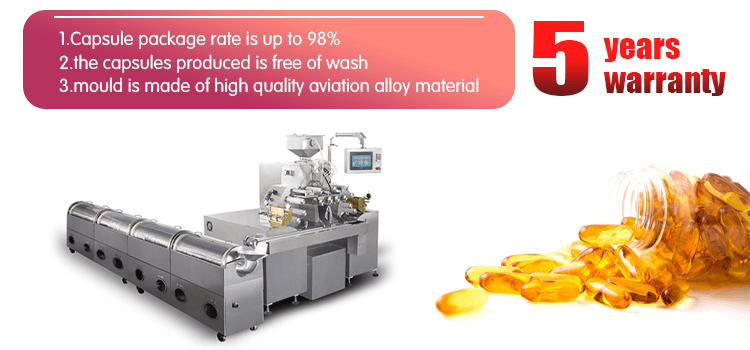
Key Steps in Softgel Manufacturing
1. Gelatin Preparation
Once dried, the capsules undergo rigorous inspection to identify and remove any defective products. This includes checking for size uniformity, proper sealing, and the absence of leaks.
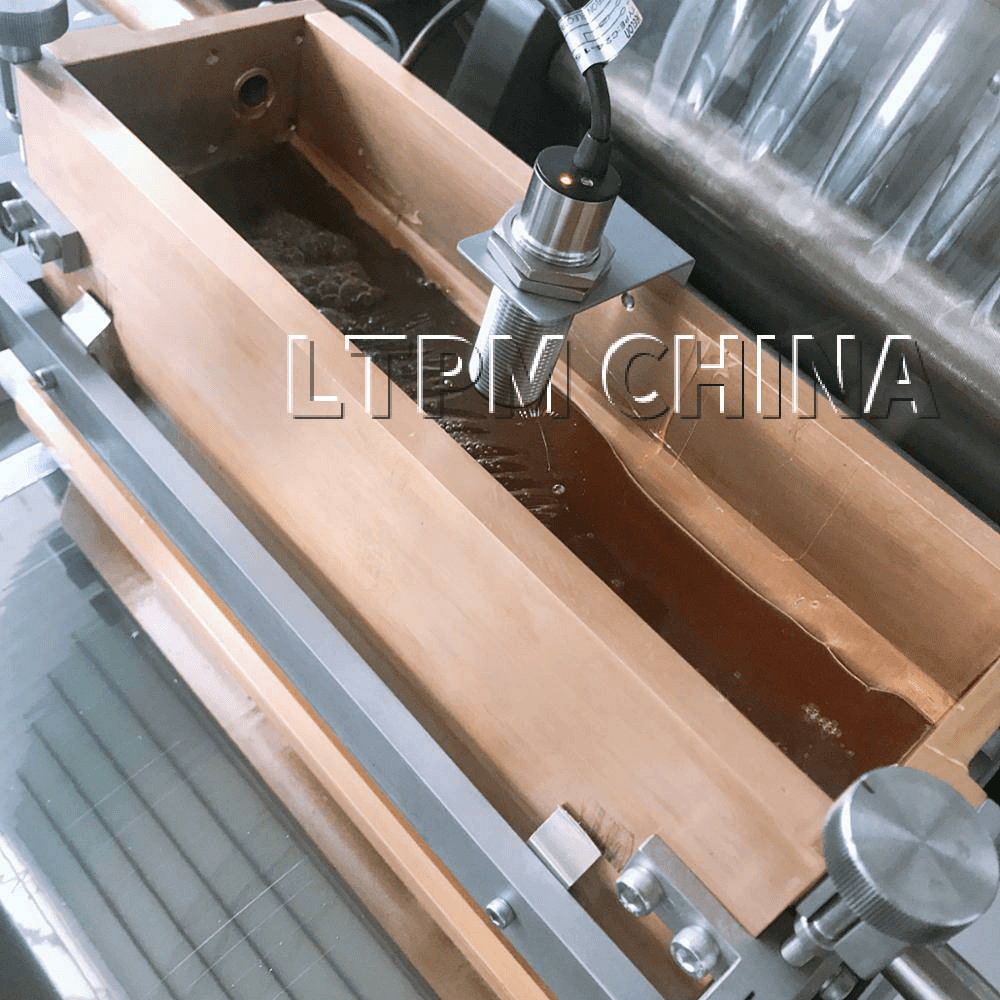
2. Fill Material Preparation
The active ingredients, which can be in liquid, semi-solid, or suspension form, are prepared in parallel. This mixture is carefully homogenized and often vacuum-processed to remove air bubbles, ensuring uniformity in the final product.
3. Encapsulation
The most crucial step is encapsulation, typically performed using a rotary die machine. Gelatin ribbons are formed, lubricated, and fed through die rolls where the fill material is injected into the gelatin shell. The two halves of the shell are sealed together under heat and pressure to form the softgel capsules.
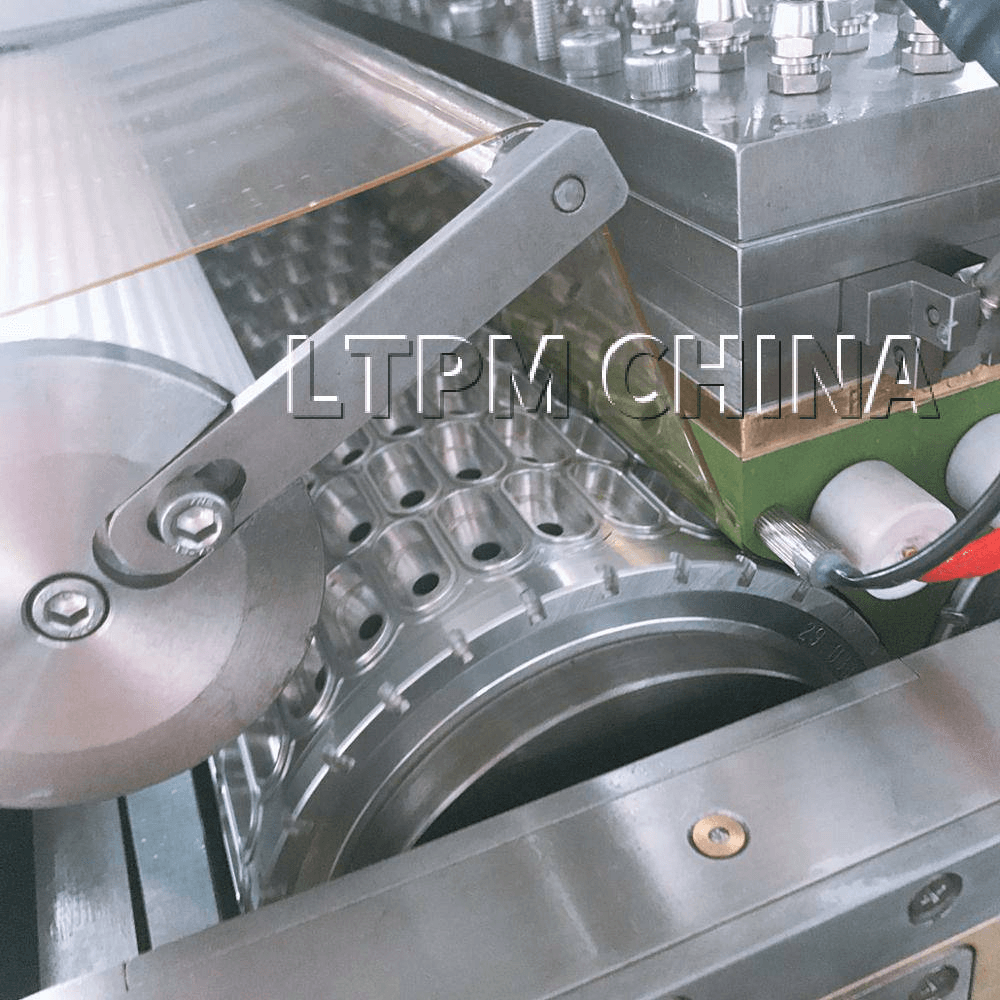
4. Drying
After encapsulation, the softgels are dried to remove excess moisture. This step is critical for maintaining capsule integrity and preventing microbial growth. The drying process often involves both tumble dryers and drying tunnels, with careful control of temperature and humidity.
5. Inspection and Quality Control
6. Polishing and Packaging
Finally, the capsules are polished to remove any residues and improve their appearance before being packaged for distribution.
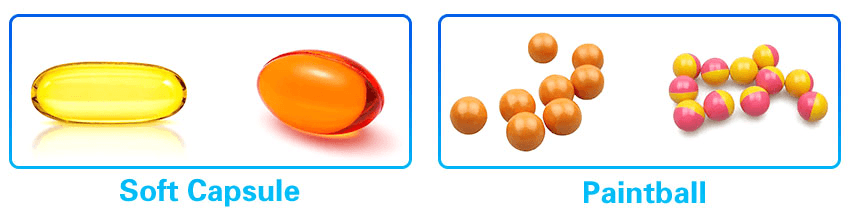
Quality Considerations in Softgel Manufacturing
Ensuring the quality of softgel capsules involves selecting the right type of gelatin and controlling variables such as moisture levels during drying. The choice of excipients and encapsulation conditions can significantly impact the stability and bioavailability of the active ingredients. Advanced technologies, like optimized gelatin formulations, can reduce common issues such as cross-linking, which can impair capsule performance.
The softgel format is particularly advantageous for delivering low-solubility drugs and other sensitive ingredients due to its ability to enhance bioavailability and mask unpleasant tastes and odors.
For manufacturers considering entering the softgel market, it's essential to invest in high-quality equipment and adhere to Good Manufacturing Practices (GMP) to produce consistent, high-quality products. This process, while straightforward in concept, requires precise control and expertise at each stage to ensure the final product meets the stringent standards required in the pharmaceutical and nutraceutical industries.