If you want to start the tablet press busuiness, or you are a pharmacist, researcher, scholar, or you are an expert in tablet press industry, this is the encyclopedia about tablet compression you need.
It covers almost all the knowledge about the tablet press.
If you have questions, please CONTACT US NOW!
Then let's get started:
1. What Is a Tablet Press Machine?
2. Tablet Making Process
3. Basic Components of Tablet Press Machine
4. Types of Tablet Press Machine
5. Tablet Press Machine Tooling
6. What Is a Single Station Tablet Press?
7. Who Is the Single Punch Tablet Press Machine Suitable For?
8. Operation of The Single Station Tablet Press Machine
9. Basic Parts of a Single Station Tablet Press
10. How does a single station tablet press machine work?
11. Maintenance Knowledge of Single Station Tablet Machine
12. What Is a Multiple Station Tablet Press Machine / a Rotary Tablet Press Machine?
13. Regulating Mechanism of Automatic Rotary Tablet Press Machine
14. Main Features For a Rotary Tablet Press
15. How Do Pharmaceutical Manufacturers Choose Tablet Press Machines?
16. Maintenance Instructions For Rotary Tablet Press
17. How Much Does a Tablet Press Machine Cost?
18. Does LTPM Offer a Tablet Production Line?
19. What Is the Features of ZP-Series Tablet Press Machine?
20. What Is the Features of GZPK-Series Tablet Press Machine?
21. What Is the Difference Between ZP-Series Tablet Press Machine and GZPK-Series Tablet Press Machine?
22. What Service Will You Get from LTPM
1. What Is a Tablet Press Machine?
A tablet press machine is used to compress pharmaceutical powder formulations into tablet form, creating tablets of uniform size, shape and weight.
The tablet press may also be used for the manufacture of products in the form of tablets for other sectors such cosmetics, cleaning products and catalysts for the petrochemical industry.
A tablet press machine is also known as:
- Tablet Compressing Machine
- Tablet Compression Machine
- Tableting Machine
- Pill Press Machine
- Pill Making Machine
- Tablet Making Machine
- Tablet Punching Machine
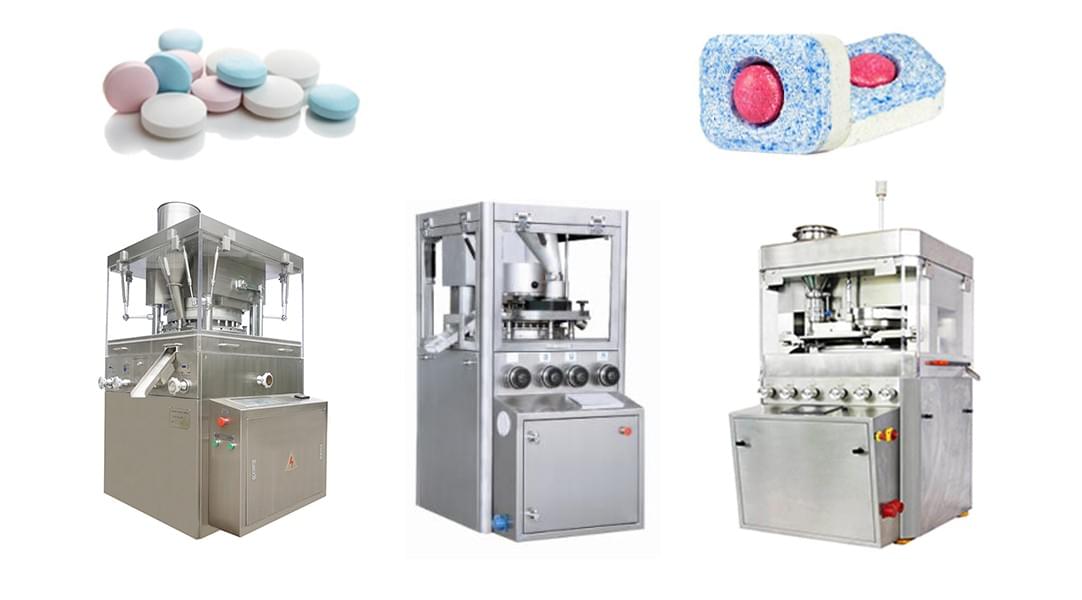
Tablet Press Machines
2. Tablet Making Process
The tablet making process starts with the formulation of powder. It is usually a mixture of several components.
For pharmaceutical products, these include the active pharmaceutical ingredient (API) and drugs, and various inactive but essential excipents, which include diluents, lubricants and binders.
The powder may undergo a process of granulation to achieve the required particle size distribution before it is fed to a tablet press machine.
The powder is fed into a hopper on the tablet press machine from where it is metered into a cavity formed by a die and two punches (an upper and lower punch).
The dies and punches, usually known as the tablet press tools, are what define the size and shape of the finished tablets.
Force is applied to the punches which press on the powder to fuse materials together and create a solid tablet form
3. Basic Components of Tablet Press Machine
- Hopper - it holds the materials that are to be compressed.
- Die - it is the cavity that defines or moulds the size and shape of the powder
- Punches - the punches compress the materials within the die
- Cam track - this helps or guides the movement of the punches
- Feeding mechanism - it moves the materials from the hopper to the die.
4. Types of Tablet Press Machine
Single Station
Single station tablet press is also known as a single punch or eccentric tablet press.
Single punch tablet press machine is the simplest one of all types of tablet making machines.
The machine uses a single tooling station that has a die and a pair of upper and lower punches.
It can be operated by hand or by an electric motor.
The compression force is exerted by the upper punch only - the lower punch is stationary during the compression step.
Multiple Station
Multiple station tablet press machines are also know as rotary tablet press, or rotary tablet press machines.
The distinguishing features of the rotary press are the die table, the turrets that hold the punches, and the cams, the cam tracks that control the punches, and the tablet ejection process.
In the rotary tablet press machine, many dies are located near the edge of the large circular die table that is able to rotate horizontally.
The upper and lower punches that correspond to each of the dies are located on turrets above and below the die table.
As the die table rotates, the cams above the upper turret and below the lower turret cause the punches to move up or down appropriately in such a way that
a. The lower punch is stationary for the compressive step when the upper punch forces down on the powder which compresses it into a tablet.
b. Once the tablet is formed, the upper punch withdraws upwards. And at the same time the lower punch also rises so as to eject the newly formed tablet from the die.
c. As the head of the machine rotates, the fixed cam tracks controls the filling, compression, and the ejection process.
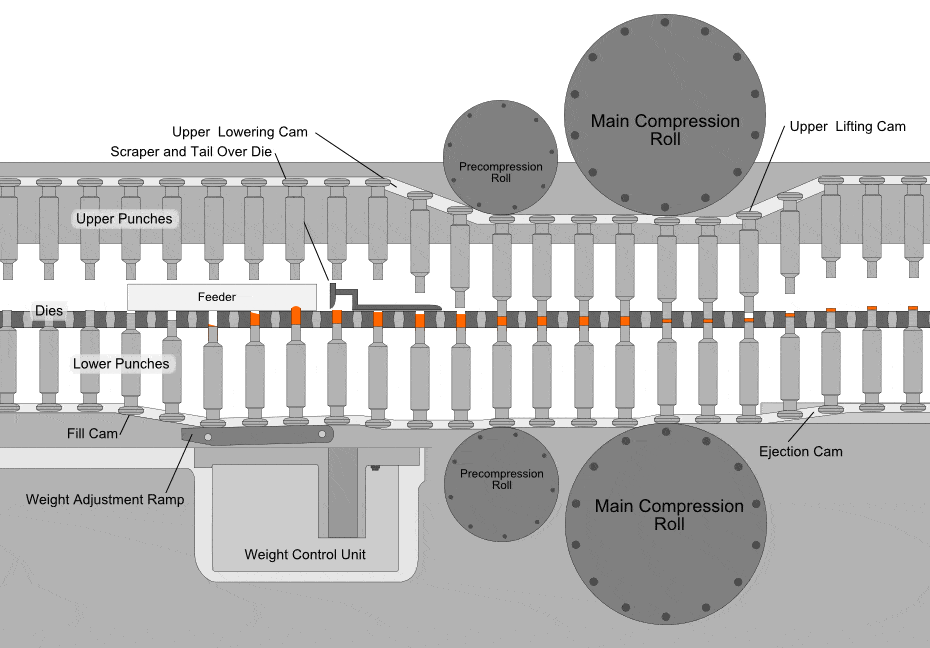
Tablet Press Animation
5. Tablet Press Machine Tooling
Details can be found in this article, let’s get started:
The size, shape and the identification marks of the tablet are determined by the compression machine tooling, i.e., the punches and dies.
The tooling must meet the specific requirements to satisfy the needs of dosage uniformity, production efficiency and aesthetic appearance.
Internationally there are two recognized standards for tablet compression tooling: the TSM standard and the EU standard.
TSM is acronym for the ‘Tablet Specification Manual’, widely recognized and exclusively used in the United States.
But the EU or ‘European Standard’ is probably more widely used than the TSM standard.
Based on the TSM and EU standards, tablet tooling is mainly classified as B tooling and D tooling.
The B tooling punches and dies can be further classified as BB, B, and D tooling can also be used on B tooling machine that is also called as DB.
6. What Is a Single Station Tablet Press?
In the pharmaceutical industry, the single station tablet machine can be said to be an indispensable processing equipment, usually used to compress various Chinese medicine tablets, western medicine tablets, etc.
A single station tablet press, also known as single punch tablet press machine is a simple mechanical machine that can be used to compress powder into tablets that are uniform in size, shape and weight.
A single station tablet press machine uses a single tooling station that has a die and a pair of upper and lower punches.
And It can be operated by hand or by an electric motor.
The machine is used for low-volume production of tablets for a wide range of applications from cosmetics and pharmaceuticals to cleaning products.
7. Who Is the Single Punch Tablet Press Machine Suitable For?
Unlike larger industrial machines, a single station table press is useful for production of relatively low-volumes of basic shaped tablets.
It is therefore well suited for
- R&D departments that need to produce small batches of new materials,
- or compounding pharmacists that need to test new formulations,
- or suppliers of nutraceuticals, supplements or herbal remedies that require a low-cost method of producing relatively small batches of products.
This type of tablet press is used for a wide variety of applications on account of the low cost and versatility.
Single station tablet press machines are also used, for example, in the production of industrial catalysts for the petrochemical industries.
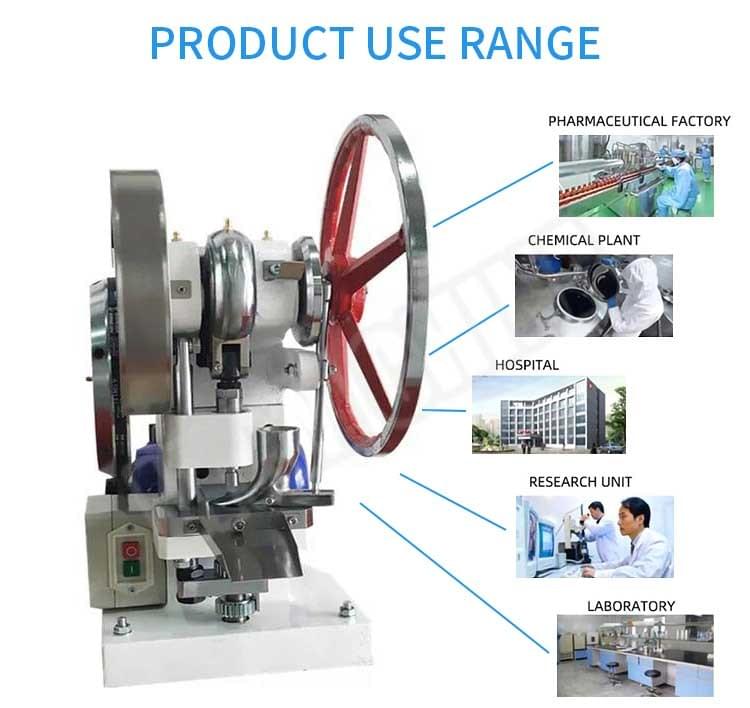
Using Range of a Single Station Tablet Press Machine
8. Operation of The Single Station Tablet Press Machine
In this type of single station tablet press machine, tablets are made by compressing powders in a single die, with a punch or stamp.
The formulation of powder is entirely depended on the intended application.
Pharmaceuticals, for example, employ a mixture of ingredients for the powder - the active pharmaceutical ingredient (API), one or more inert excipients, lubricants and disintegrators.
The single punch tablet press machine can be hand operated or it can be motorised.
In the former case, tablets are made one at a time. In the latter case, tablets can be made at in small production which runs typically at a rate of 5000 tablets per hour.
9. Basic Parts of a Single Station Tablet Press
A typical single station tablet press commonly features the following basic components:
- Hopper: It holds the granules and powder that need to be compressed. Powder and granule material falls by gravity from the hopper into the die.
- Die: It provides a mold that makes the compressed material in the form of the desired shape. The base of the die is formed by the lower punch and it is the upper punch that descends onto the loose powder and compresses it.
- Upper and lower punches: The upper punch provides the compressive force to bind the powder granules into a tablet. The lower punch acts as a base for the die and is raised at the end of the compression phase to eject the tablet from the die.
- Cam track: It is the mechanical gear that guides the movements of the two punches.
- Capacity regulator: It regulates the depth of loose powder in the die by adjusting the depth of the lower punch.
- Ejection regulator: It regulates the lower punch so that when it is raised at the end of the compression, the punch is level with the surface of the die, enabling the finished tablet to be swept aside into the collecting vessel.
- Driving wheel: It guides the movement of the upper and lower punches and the hopper.
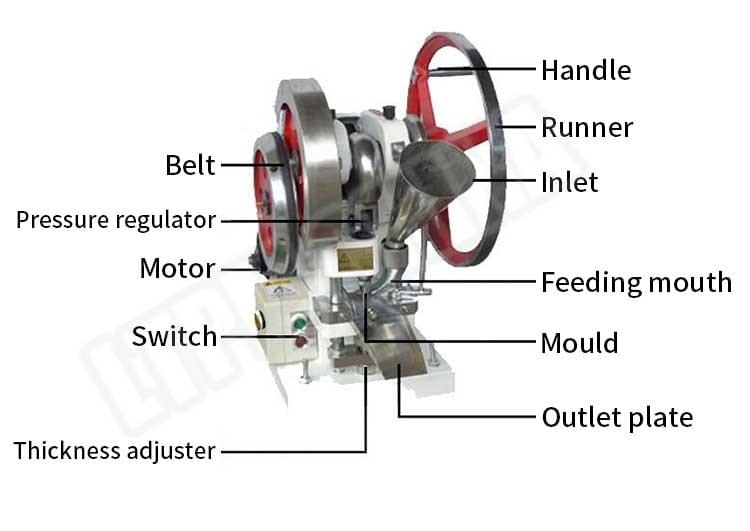
Basic Parts of a Single Station Tablet Press Machine
Note that in a single station tablet press machine, there is only one upper and lower punch and die set.
Force for compressing the tablet is exerted only through the upper punch, while the lower punch is stationary for the period of compression.
The powder material compacted by the pressure exerted between the moving upper punch and the lower stationary punch.
The shape of the tablet is depended on the shape of the die cavity.
10. How Does a Single Station Tablet Press Machine Work?
A single station tablet press produces tablets through a number of steps that can be described as follows:
- Filling: the upper cam withdraws the upper punch from the die, and the lower punch is low inside the die cavity so that the powder falls from the hopper and fills the cavity that made by the die and bottom punch. The lower punch is then adjusted to the required weight of material and, as it lifts, excess powder is ejected from the die.
- Compression: the lower punch remains stationary and the upper punch lowers into the die to compress the powder into a tablet.
- Ejection: the upper punch is then withdrawn while the lower punch pushes upwards lifting the formed tablet from the die. The tablet is then removed from the die surface by the surface plate.
- Then, the cycle is repeated for the next batch.
The single station tablet press is adjusted to suit the type of tablet, the material, compression and capacity of material required for each tablet.
Adjustments are usually made by operating the machine manually so that a check can be made on the appearance, size and mechanical robustness of the formed tablets.
Once the operator is satisfied with the quality of the tablet, the mechanical adjustments are locked into place, and the machine is ready for automatic production.
It is important that settings are checked regularly especially if large quantities of tablets are made, to maintain the quality and standard of the product.
11. Maintenance Knowledge of Single Station Tablet Machine
In addition to mastering the use matters, single station tablet press machine maintenance is also a "learning".
It looks simple, but the actual operation is not easy.
According to the industry, there are the following maintenance techniques for single punch tablet press machines.
- First, the user must manually test and press a few tablets before and after the equipment is working, and then turn on the electric press after there is no problem.
- Second, the issue of cleanliness needs attention. After using, the user should take out the remaining powder and wipe all parts of the machine.
- If the single station tablet press machine is out of service for a long time, the die must be removed, the working surface of the equipment must be wiped clean, coated with anti-rust oil, and dust-proof clothing.
- The die should be cleaned and immersed in oil for storage.
- Third, the lubrication of the friction surfaces of the moving parts is an important step to ensure the normal operation of the machine and prolong the service life.
- The industry pointed out that, especially the main moving parts, if single station tablet press machines are running under the condition of lack of oil, they may quickly be damaged.
- Therefore, before using the single punch tablet press, all oil cups, oil holes and friction surfaces must be lubricated and cleared.
- When a single station tablet press is running, each friction surface is covered with oil film before it can be put into use.
- Fourth, check the parts regularly.
- Before each work, check whether the screws are loose or not, and always pay attention to checking during the work.
- If screws are loose, they should be tightened immediately to avoid malfunction.
- Fifth, in the process of tablet pressing, the operator must frequently check the quality of the punching die.
- If there are missing edges, cracks, deformation, etc., they should be replaced in time to avoid malfunction, damage to the machine, and affecting the quality of the tablet.
12. What Is a Multiple Station Tablet Press Machine / a Rotary Tablet Press Machine?
It is a type of tablet press machine with numerous tooling stations in constant rotation to make different types of tablets.
Rotary tablet press is a kind of automatic rotation, continuous tablet press miniaturization machine, equipped with overload protection device, when the pressure overload can automatically stop.
The rotary tablet press improves the uniformity of the tablet density and reduces the phenomenon of crack loosening.
You can refer to it as an automatic rotary tablet press machine.
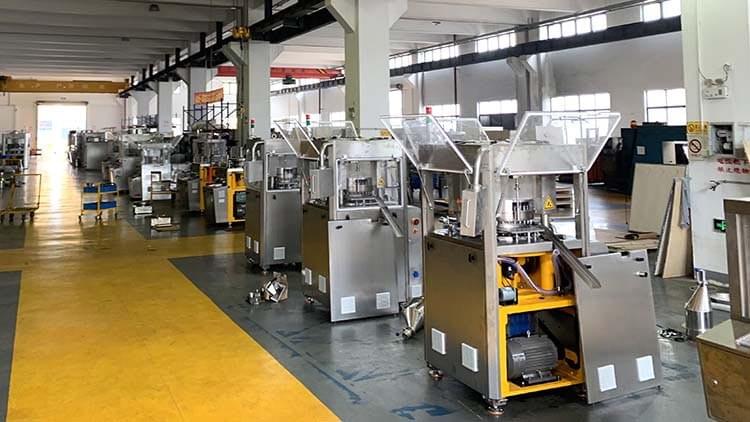
Multiple Station Tablet Press Machine (Rotary Tablet Press Machine)
13. Regulating Mechanism of Automatic Rotary Tablet Press Machine
Filling Regulating Mechanism
The filling dose adjustment on the rotary tablet press is mainly based on the filling rail.
By rotating the dial regulating plate, the shaft can be driven to rotate, and the worm shaft connected with it also rotates.
When the worm wheel rotates, the internal threaded hole causes the lifting rod to move in an axial direction, and the filling rail which is firmly connected with the lifting rod also moves up and down accordingly.
That is to adjust the position of the downward punch in the middle die hole, so as to meet the requirements of adjusting the filling quantity.
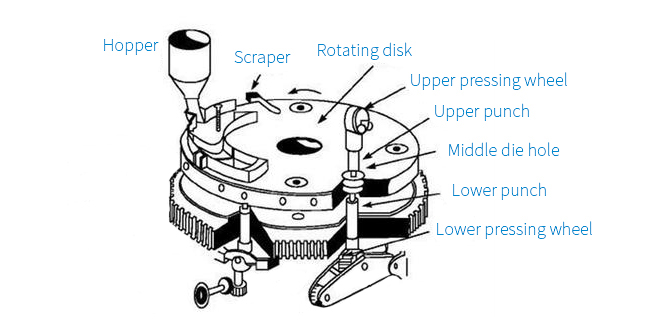
Basic Parts of Rotary Tablet Press Rotating Disk
There are three commonly used hopper feeding methods for rotary tablet presses: Open forced feeding, Closed forced feeding, and Gravity feeding.
Up and Down Running Guide Device
The axial movement of up and down is controlled by the guide rail of up and down.
The up-moving guide rail can be splice together into a rotary guide plate, which is expanded as, indicating that the machine is double-chip, and there is still the same guide rail.
The guide plate is fastened to the upper part of the non-rotating mandrel, and the tail of the up-stroke is in contact with the curved flange of the up-stroke guide.
The cross section shape of the flange of the up-stroke guide rail will be consistent with the cross section of the up-stroke shrinkage diameter.
When the up-stroke rotates with the working wheel, it will be subject to the control of the guide rail and produce axial motion.
The downstroke guide rail is relatively simple, which is inlaid on the frame body, and the downstroke depends on the weight and pressure of the upstroke on the downstroke guide rail surface.
According to the force of the object in the die, the up-rushing downward guide rail is designed according to the cosine curve, so that the acceleration of the up-rushing is zero, in order to reduce the impact and increase the service life of the dies.
As the upstroke moves along the upstroke rail, the upstroke slowly rises from low to high, gradually exits through the middle die hole, and reaches the highest point.
As the upstroke begins to walk in parallel tracks, the downstroke rises on the upstroke, gradually reaching the highest point, and ejecting the tablets.
When the upper charge stays at the highest point in the downward rail, the lower charge starts to fall, and then the lower charge runs on the filling rail.
During this period, the middle die hole is completely exposed to the covering area of the feeder, completing the feeding process.
When the upper punch reaches the control area of the downward rail, the upper punch gradually descends into the middle die hole for the tablet pressing process.
At this time, the lower punch is at the lowest point but does not leave the middle die hole, so the bottom of the hole is always sealed.
Pressure regulating mechanism
The actual application of pressure to a drug on a rotary tablet press does not depend on the running rail.
The upper and lower rushing are placed on a pair of upper and lower rollers on the rack during the pressurization stage (at this time, the upper rushing tail is separated from the upper rushing rail).
The eccentric regulating pressure mechanism is an eccentric regulating pressure mechanism.
The upper pressing wheel is mounted on an eccentric shaft. By adjusting the nut, the pressure of the compression spring is changed, and the swing Angle of the rocker arm is changed at the same time, so as to change the eccentric bearing of the eccentric shaft, and to reach the lowest point position of adjusting the upper press wheel, and thus change the lowest point position of the upper thrust.
When the pressure of the die is too high, the buffer spring will bear too much force, which will make the micro switch move and stop the machine, thus achieving the function of overload protection.
Another kind of pressing wheel eccentric adjusting mechanism, when loosening the setting screw, using the plum handle to rotate the worm shaft, rotating the worm wheel, can also change the eccentric axis eccentric azimuth, in order to achieve the purpose of changing the highest position of pressing wheel, so as to adjust the highest position of pressing plate at the moment.
The upper and lower pressure wheels are mounted on the upper and lower pressure wheels respectively.
One end of the diamond pressure wheel stand is connected with the regulating mechanism respectively, and the other end is connected with the fixed bracket.
Adjusting the handwheel can change the upper and lower position of the upper press wheel frame, so as to adjust the depth of the upper punch into the middle die hole.
Adjust the thickness of the tablet by adjusting the handle so that the roller can move up and down to adjust the thickness and hardness of the tablet.
The pressure is controlled by the pressure cylinder.
This kind of pressure and pressure regulating mechanism can ensure the pressure increase stably, and can maintain a certain time at the maximum pressure.
It has a certain effect on the compression of granular materials and the discharge of air, so it is suitable for high-speed rotary tablet press.
14. Main Features For a Rotary Tablet Press
- Multi-station tablet press machine has numerous stations for producing tablets.
- The output of the rotary tablet press is higher than that of the single-punch tablet machine, and the speed of the rotary tablet press is faster.
- Production of a variety of discs and shaped pieces.
- The doors and windows equipped with transparent glass can clearly observe the state of lamination and prevent pollution.
- The side panel can be fully opened for easy internal cleaning and maintenance.
- The parts in contact with drugs are made of stainless steel by precision machining, which can maintain the surface luster and prevent cross contamination, and meet the GMP requirements.
- The support frame is made of aluminum alloy, which can be disassembled independently for transportation.
- The layout of all controllers and operating parts is reasonable.
- Frequency conversion speed regulation device is used for electrical speed regulation, which is convenient to operate, stable to rotate, safe and accurate.
- Implement mechatronics.
15. How Do Pharmaceutical Manufacturers Choose Tablet Press Machines?
Details can be found in this article, let’s get started:
Pharmaceutical manufacturers should consider the following factors in selecting tablet press:
The Variety, Grade and Added Value Level of the Products Produced
If tablet makers produce better products and higher added value, they can choose high-end equipment.
After all, this kind of equipment has good performance and high degree of automation, which can ensure the product quality.
The Size of the Shift Output
When selecting equipment, it is not necessary to blindly pursue the output of a single machine, but to determine the output of a single machine according to the actual shift output demand.
Workshop Area
If the layout area of the workshop is relatively large, the medium and low speed tablet press can be used.
The number of equipment of tablet press manufacturers can be increased appropriately, so as to reduce the equipment investment.
If the equipment layout in the workshop is very compact, the sub high speed or high speed tablet press can be selected.
Although the investment is relatively high, the difficulty of equipment layout is avoided.
However, no matter the size of the area, the tablet maker thinks that at least two tablet presses should be arranged under normal conditions.
16. Maintenance Instructions For Rotary Tablet Press
- Regularly check the parts of rotary tablet press machine once or twice a month. The inspection items are whether the worm gear, worm, bearing, pressing wheel, crankshaft, upper and lower guide rail and other moving parts rotate flexibly and wear.
- If any defect is found, it should be repaired and used in time.
- After one use or shutdown, take out the residual powder and brush off the residual powder of the machine.
- If the machine is out of service for a long time, remove all the dies and wipe the machine clean.
- The smooth surface of the machine shall be coated with anti rust oil and covered with cloth awning.
- The maintenance of the die should be placed in the iron box with cover, so that the die is completely immersed in the oil and kept clean, so as not to rust and bruise.
- The customized iron box can be packed in one box with each specification, which can avoid wrong installation and help to master the damage situation.
- The place of use should be cleaned frequently, especially for the manufacture of medicine and edible tablets.
17. How Much Does a Tablet Press Machine Cost?
The price of the tablet press machine varies depending on the type of tablet press.
Generally speaking, the price of a simple single-punch tablet press machine ranges from 1,000 US dollars to 3,000 US dollars.
The higher the speed and output of the tablet press, the higher the price.
The price of small and medium-sized rotary tablet presses on the market ranges from 3,000 US dollars to 100,000 US dollars.
And the price of high-speed and high-volume tablet presses will be higher.
LeadTop Pharmaceutical Machinery China (LTPM CHINA) also provides single station tablet press machine.
If you are interested in a single punch tablet press machine, you can go to the LTPM to find a single punch tablet press machine you like.
LeadTop Pharmaceutical Machinery China (LTPM CHINA) provides multiple station tablet press machine (rotary tablet press), too.
18. Does LTPM Offer a Tablet Production Line?
Yes, LTPM offers a whole production line for tablets from powder making and granulation, tablet press, to packing.
LTPM is a professional company specializing in pharmaceutical industry since 1996.
LTPM has extensive experience in oral solid dosage preparations (osd).
The solution capability of LTPM is at the leading level in the industry.
In LTPM, you can choose any model for tablet press with various capacity and applications.
Here are some popular models you will get from LTPM:
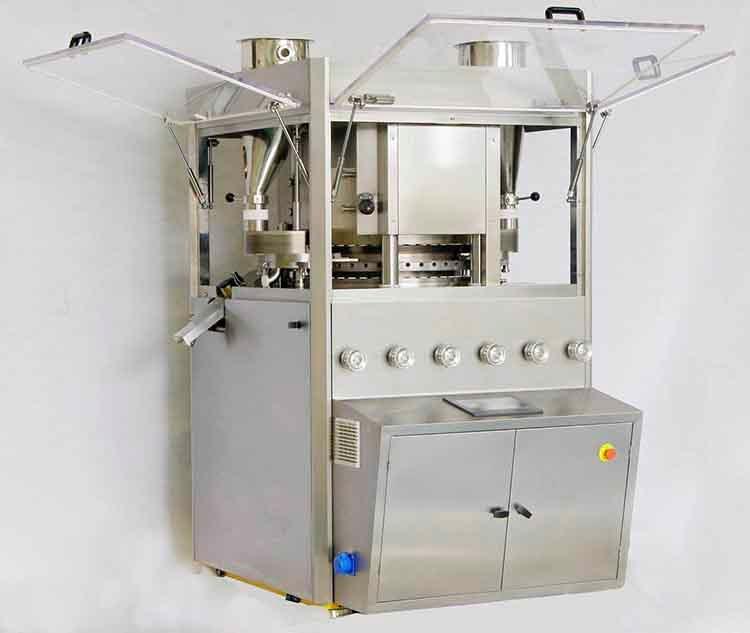
GZPK-Series High Speed Tablet Press Machine
19. What Is the Features of ZP-Series Tablet Press Machine?
- The ZP-series tablet press machine adopts Germany, Japan and Denmark brand electronics for PLC, touch screen, inverter, Relays and contactors. So it is Stable working with simple maintenance.
- The material of the ZP-series tablet press machine is made of stainless steel with totally closed, the surface of turntable deal with polished and prevent cross pollution which meet the GMP standard.
- ZP-series tablet press machine is equipped with Organic-glass perspective window for tablet producing observation. Each perspective window could be fully opened and easy for cleaning and maintenance.
- ZP-series tablet press machine is adopts the import Frequency Timing with Electromagnetism Clutch.
- Driving system is equipped with oil box and running under oil, easy for heat dissipation and wear-resistance.
- ZP-series tablet press machine is equipped with Dust Collector as well, which avoids the dust emission, and recycle to save dust.
20. What Is the Features of GZPK-Series Tablet Press Machine?
- Double-sided discharge chutes, high productivity.
- No handwheel with machine, automatic drive by synchronous motor, it can complete realize automatic production.
- Separate control cabinet to operate machine, separated production area from operation area to ensure the safety for operator and sanitation for production.
Adopts encoder to count, measure and display control is accurate.
- Main pressure system, pre-pressure system, filling system, feeding system adopt modular design.
- Simple structure. These modular parts can be freely adjusted or removed. Non-interference between maintenance are easy.
- The main pressure and pre-pressure are the same structure which can be interchanged each other.
- Both main pressure and pre-pressure are all 100kn which make it easier for forming tablets.
- Tri-wheeled double layer feeding system.
- The upper impeller can increase powder flow and balance powder density.
- The lower impellers are used for feeding and dosing to ensure the uniformity of feeding.
- Use servo motor to adjust dosing cam track which an control filling depth to ensure accurate dosing.
- Force-feeding device controls the flow of powder and ensures the accuracy of feeding.
- Feed is easy to be disassembled and platform is easy to be regulated.
- No dead area in press chamber and easy to be observed and cleaned.
21. What Is the Difference Between ZP-Series Tablet Press Machine and GZPK-Series Tablet Press Machine?
The rotation speed of turret is different, which reaches 25 rpm for ZP tablet press machine, but 80 rpm at max for GZPK tablet press machine.
So GZPK-series tablet press machine is a typical high speed tablet press.
The capacity is different. The capacity of ZP tablet press machine is 150,000 tablets per hour in maximum.
The capacity of GZPK tablet press machine is 470,000 tablets per hour in maximum.
22. What Service Will You Get from LTPM?
LTPM has seven technicians who gets passport ready to travel all over world to offer service to you.
LTPM provides 24 hours hot line for Technical Support.
LTPM gets 18 hours internet line for technical support.
Video camera in workshop to help you adjust and solve machine problem in working situation.
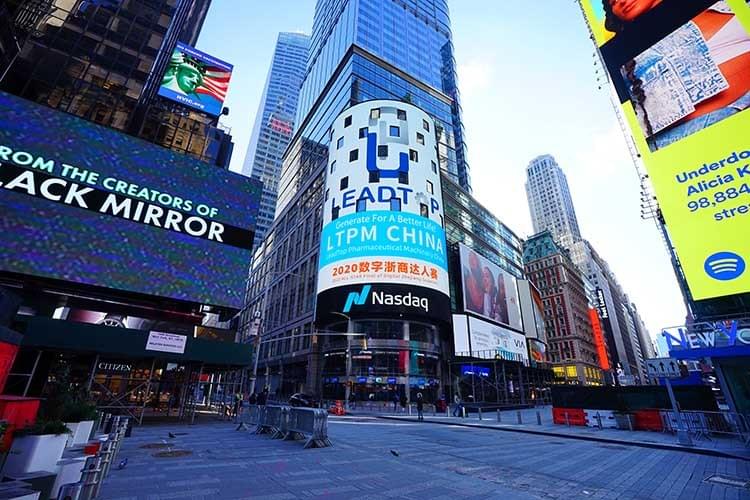
LTPM Nasdaq Screen Display
If you have questions,
please CONTACT US NOW!
Written & Copyright by Steve Chen