A tablet compression machine is a vital piece of equipment in pharmaceutical manufacturing, used to compress powder into tablets of uniform size and weight.
The principle of a tablet compression machine involves compressing a powder mixture into a solid tablet by applying pressure using punches and dies within the machine. The process ensures uniformity in tablet size, shape, and weight, which is essential for dosage accuracy in pharmaceutical applications.
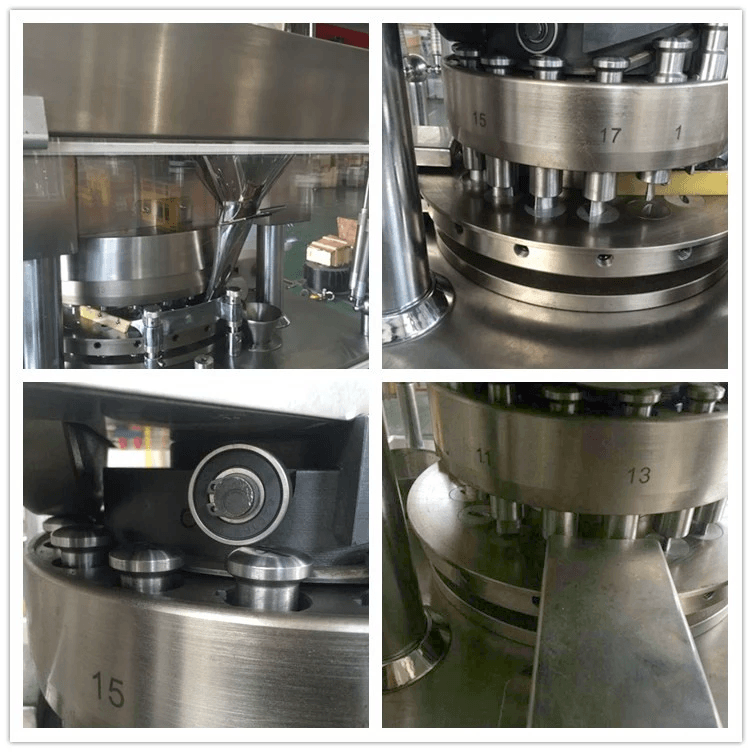
A tablet compression machine operates on a straightforward yet precise principle: compressing powdered material into solid tablets. This is achieved through several key steps:
1. Filling: The powder or granule mixture is filled into a die cavity from a hopper. The die is a hollow cavity where the tablet's shape is formed.
2. Compression: The upper and lower punches descend into the die cavity, applying pressure to compress the powder mixture into a solid form. The amount of pressure applied is carefully controlled to ensure uniformity and consistency in the tablet's size and hardness.
3. Ejection: After compression, the lower punch moves up to eject the formed tablet from the die cavity. The tablet is then pushed out of the machine, usually onto a conveyor belt for further processing or packaging.
4. Tooling: The punches and dies are crucial components, as they determine the shape, size, and imprint of the tablet. Different sets of tooling can be used to produce tablets of various designs and specifications.
Understanding the tablet compression machine's operation is essential not only for producing high-quality tablets but also for maintaining the equipment and troubleshooting any issues that may arise. With this foundational knowledge, we can delve into related topics that address more specific aspects of the tablet compression process.
1. What factors influence the quality of tablets produced?
Tablet quality is influenced by factors such as the uniformity of the powder blend, the accuracy of the die filling, the pressure applied during compression, and the wear and tear on the machine's tooling. Consistent monitoring and calibration are essential to maintain high-quality output.
2. How do you maintain a tablet compression machine?
Regular maintenance includes cleaning the machine to prevent contamination, inspecting and replacing worn tooling, lubricating moving parts, and calibrating the compression settings. Proper maintenance ensures the machine operates efficiently and produces high-quality tablets.
3. What are the common issues in tablet compression, and how can they be resolved?
Common issues include tablet sticking, capping, and weight variation. These can often be resolved by adjusting compression pressure, ensuring proper lubrication of the machine, and maintaining consistent powder granulation.
4. How does the design of punches and dies affect tablet production?
The design of punches and dies directly affects the tablet's shape, size, and imprint. Custom tooling can be created for specialized tablet designs, but it requires precise manufacturing to ensure consistent tablet production.
5. What is the role of pre-compression in tablet manufacturing?
Pre-compression is a step where the powder mixture is lightly compressed before the final compression. This helps in expelling air from the powder and ensuring better cohesion of the material, leading to higher quality tablets.
The principle of a tablet compression machine is foundational to producing consistent, high-quality tablets in the pharmaceutical industry. By understanding and controlling the compression process, manufacturers can ensure the tablets' uniformity in size, weight, and active ingredient distribution, which is crucial for patient safety and product efficacy.
For further insights into optimizing your tablet compression process or to explore our range of tablet compression machines with customizable features, contact us today. Take advantage of our current promotions, including extended warranties and discounts on bulk orders!