Maintaining consistent filling accuracy over multiple production batches and extended operating cycles is crucial for pharmaceutical manufacturing. Variations in batches and prolonged use of machinery can impact the stability and accuracy of the filling process.
Yes, filling accuracy can be affected by production batches and operating cycles. Ensuring long-term and stable filling effects requires regular maintenance, calibration, and monitoring of the capsule filling machine.
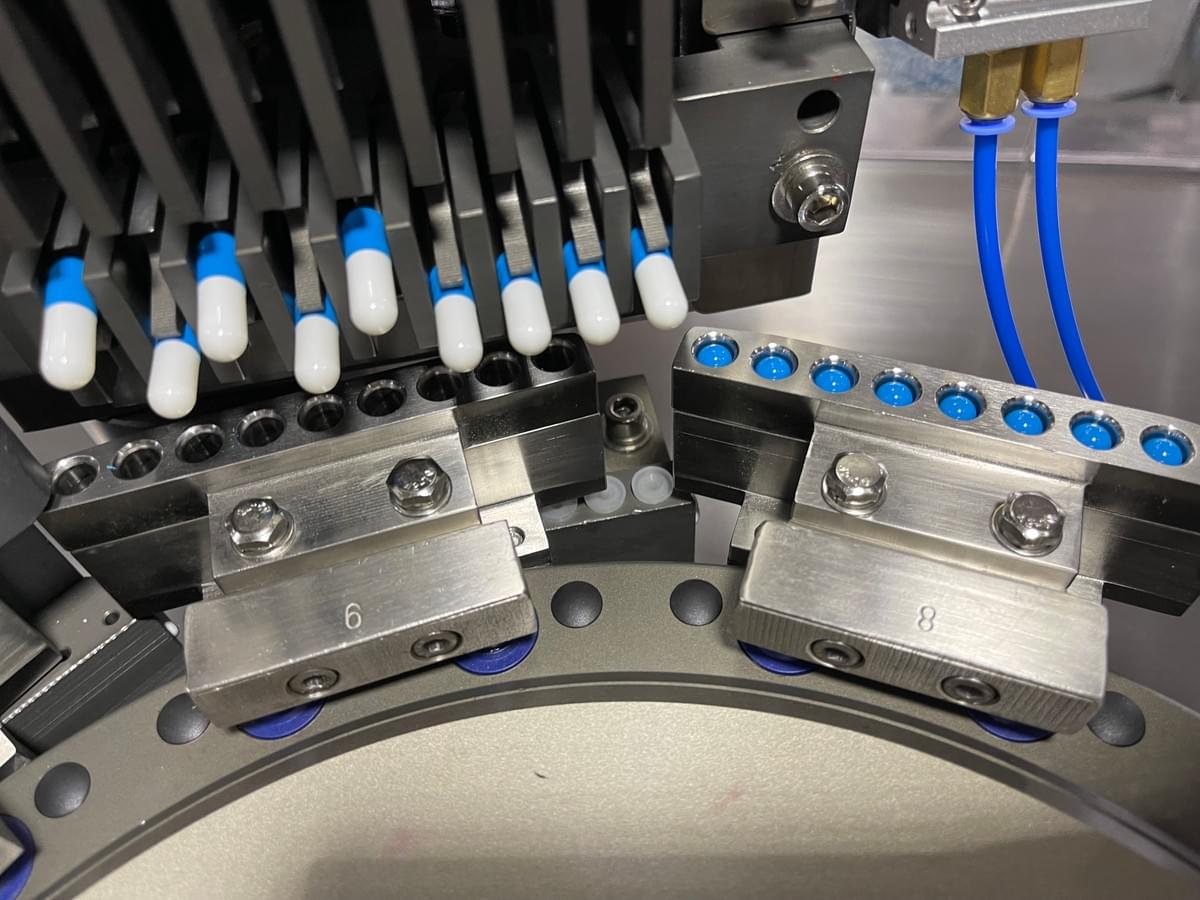
Filling accuracy is vital for ensuring the quality and efficacy of pharmaceutical products. Over time, the performance of capsule filling machines can degrade due to various factors associated with production batches and operating cycles. Here’s an in-depth look at how these factors affect filling accuracy and how to ensure stable performance:
Impact of Production Batches:
Variation in Raw Materials: Different production batches may have variations in raw material properties such as particle size, moisture content, and density. These variations can lead to inconsistent flow and fill weights.
Batch-Specific Calibration: Each new batch may require specific calibration settings to achieve the desired filling accuracy. Failure to adjust the machine settings can result in inaccuracies.
Quality Control: Implementing stringent quality control measures for each batch helps in identifying and addressing variations early in the process.
Effect of Operating Cycles:
Machine Wear and Tear: Continuous operation over extended periods can lead to wear and tear of machine components such as dosing disks, tamping pins, and encapsulation units. This wear can cause deviations in fill weight and consistency.
Temperature and Humidity Changes: Environmental factors such as temperature and humidity can fluctuate over time, affecting the flow properties of the powder and the performance of the machine.
Maintenance Schedule: Adhering to a regular maintenance schedule is essential for replacing worn parts, lubricating moving components, and ensuring the machine operates within specified tolerances.
Ensuring Long-Term Stability:
Regular Calibration: Periodic calibration of the capsule filling machine is crucial. Calibration involves adjusting the fill weight, tamping pressure, and other parameters to match the current production batch properties.
Preventive Maintenance: Implementing a preventive maintenance program helps in identifying potential issues before they lead to significant problems. This includes regular inspection, cleaning, and replacement of worn parts.
Environmental Control: Maintaining a controlled environment in terms of temperature and humidity helps in stabilizing the filling process. Using dehumidifiers and climate control systems can mitigate the effects of environmental fluctuations.
Ensuring consistent filling accuracy over multiple production batches and operating cycles involves a combination of proper calibration, maintenance, and environmental control. Let's explore related topics that delve deeper into strategies and techniques for maintaining long-term filling accuracy.
How to Implement an Effective Calibration Routine for Capsule Filling Machines?
Implementing an effective calibration routine involves setting a regular schedule for calibration checks and adjustments. The routine should include detailed procedures for measuring fill weights, adjusting machine settings, and recording calibration data. Using standardized calibration materials and tools ensures consistency and accuracy. Regular training for operators on calibration techniques and the importance of maintaining accurate records can further enhance the effectiveness of the routine. Consistent calibration helps in identifying drifts in machine performance and making necessary adjustments to maintain filling accuracy.
What Are the Best Practices for Preventive Maintenance of Capsule Filling Machines?
Best practices for preventive maintenance include regular inspection of all machine components, lubrication of moving parts, and timely replacement of worn or damaged parts. Developing a maintenance checklist and schedule helps ensure that all necessary tasks are performed systematically. Keeping detailed maintenance records and tracking the performance of the machine over time can provide insights into potential issues and help in planning maintenance activities proactively. Preventive maintenance reduces the risk of unexpected downtime and ensures that the machine operates efficiently and accurately.
How Does Environmental Control Affect Capsule Filling Accuracy?
Environmental control is crucial for maintaining consistent filling accuracy. Fluctuations in temperature and humidity can affect the flow properties of powders, leading to variations in fill weight. Implementing climate control systems, such as air conditioning and dehumidifiers, helps maintain stable environmental conditions. Monitoring environmental parameters continuously and making adjustments as needed ensures that the production environment remains within the optimal range for capsule filling. Consistent environmental conditions contribute to reliable and accurate filling processes.
How to Train Operators for Maintaining Filling Accuracy Over Time?
Training operators is essential for maintaining filling accuracy over time. Comprehensive training programs should cover machine operation, calibration procedures, maintenance tasks, and troubleshooting techniques. Providing hands-on training and regular refresher courses helps operators stay updated on best practices and new technologies. Encouraging operators to maintain detailed records of machine performance and issues can also help in identifying trends and making informed decisions. Well-trained operators play a critical role in ensuring consistent filling accuracy and overall production efficiency.
What Are the Common Challenges in Maintaining Filling Accuracy and How to Overcome Them?
Common challenges in maintaining filling accuracy include variations in raw material properties, wear and tear of machine components, and environmental fluctuations. Overcoming these challenges requires a proactive approach involving regular calibration, preventive maintenance, and environmental control. Implementing robust quality control measures and continuous monitoring of the filling process can help in identifying and addressing issues promptly. Investing in advanced technology and training for operators further enhances the ability to maintain consistent filling accuracy. By addressing these challenges systematically, manufacturers can ensure stable and reliable filling processes.
Filling accuracy in capsule filling machines can be affected by variations in production batches and extended operating cycles. Ensuring long-term and stable filling effects involves regular calibration, preventive maintenance, and environmental control. By implementing effective calibration routines, best practices for maintenance, and continuous monitoring of environmental conditions, manufacturers can maintain high filling accuracy and optimize their production processes.
For pharmaceutical manufacturers looking to ensure long-term and stable filling accuracy, contact us today. We offer expert consultation and advanced capsule filling machines designed to meet your specific needs. Take advantage of our special discounts on calibration and maintenance services to enhance your production efficiency and maintain consistent filling accuracy.