Filling accuracy in capsule filling machines is crucial for maintaining quality and consistency in pharmaceutical production. The characteristics and shape of the product being filled can significantly influence the accuracy of the filling process. Adjustments need to be made to cater to different products to ensure precise filling.
Yes, filling accuracy is affected by product characteristics and shape. Adjustments can be made by calibrating the machine settings such as fill weight, powder flow, and encapsulation parameters to match the specific product properties.
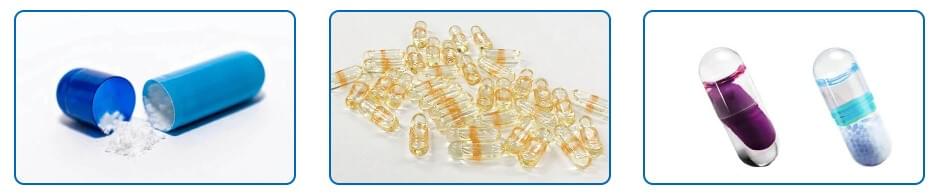
The filling accuracy of a capsule filling machine is influenced by several factors related to the product's characteristics and shape. Key factors include the particle size, flow properties, and density of the product. For instance, fine powders may have different flow dynamics compared to granules, requiring different machine settings to achieve accurate filling.
Particle Size and Shape: Products with uniform particle sizes and shapes generally flow more consistently, leading to better filling accuracy. Irregular shapes or varying particle sizes can cause uneven flow and affect the fill weight.
Flow Properties: Products with good flow properties, such as free-flowing powders, fill more accurately than those with poor flow properties. Poor flow can cause clumping and inconsistent filling.
Density: The density of the product affects the volume that can be filled into each capsule. Denser products require different settings to achieve the desired fill weight compared to less dense products.
Adjustments for Different Products:
Calibrating Fill Weight: Adjust the fill weight settings on the capsule filling machine to match the specific product being filled. This ensures that each capsule contains the correct amount of product.
Modifying Encapsulation Parameters: Adjust parameters such as tamping pressure and dosing disk settings to accommodate different product characteristics. This helps in achieving a consistent fill.
Using Different Tooling: Employ different dosing disks and tamping pins designed for specific products. This customization helps in managing the flow and fill of diverse products effectively.
Understanding how to adjust capsule filling machines for different products is essential for maintaining filling accuracy. It is equally important to ensure that the adjustments made are backed by data to track and optimize the filling process continually.
What Factors Influence the Flow Properties of Powders in Capsule Filling?
The flow properties of powders are critical in capsule filling. Factors such as particle size distribution, moisture content, and surface texture significantly influence these properties. Fine, dry powders tend to flow more easily than those with high moisture content or irregular particle shapes. Poor flow properties can cause clumping, leading to inconsistent fills and potential machine blockages. Adjusting these factors can improve flow and filling accuracy. For instance, powders with poor flow properties may benefit from the addition of flow aids or adjusting the environmental conditions, such as humidity, in the production area. Implementing these adjustments can enhance the flow characteristics and lead to more precise filling.
How to Calibrate a Capsule Filling Machine for Different Densities?
Calibration of a capsule filling machine for different product densities involves adjusting the machine settings to ensure that the correct fill weight is achieved consistently. This process begins with determining the density of the product. Once the density is known, adjustments can be made to the machine’s fill volume and tamping pressure settings. For denser products, the fill volume may need to be decreased to prevent overfilling, while less dense products may require an increase in fill volume to achieve the desired weight. Regular calibration checks are essential to maintain accuracy, especially when switching between products with different densities. Calibration ensures that the machine operates within the specified tolerances and produces capsules with consistent fill weights.
What Role Does Humidity Control Play in Capsule Filling?
Humidity control is vital for maintaining the flow properties of powders during the capsule filling process. Excessive humidity can cause powders to absorb moisture, leading to clumping and inconsistent flow. This can result in inaccurate fills and potential machine malfunctions. To prevent these issues, maintaining an optimal humidity level in the production area is crucial. This can be achieved using dehumidifiers and climate control systems. Regular monitoring of humidity levels and implementing controls to maintain a stable environment ensures that the powders retain their desired flow properties. Consistent humidity control helps achieve precise filling and enhances the overall efficiency of the capsule filling process.
How to Optimize Tamping Pressure for Different Products?
Optimizing tamping pressure is essential for achieving uniform fill in capsules. Different products require different tamping pressures based on their flow properties and fill requirements. Fine powders, for example, may require lower tamping pressure compared to granules to avoid compacting the powder too tightly, which can affect the dissolution rate of the final product. The optimization process involves conducting trials with varying tamping pressures and observing the effects on fill weight and capsule integrity. Regular testing and adjustments help identify the optimal pressure setting for each product. This process ensures that the capsules are filled uniformly and reduces the risk of capsule damage during filling.
What Are the Benefits of Using Specialized Tooling for Different Products?
Using specialized tooling in capsule filling machines offers significant benefits in terms of filling accuracy and product quality. Tooling such as custom dosing disks and tamping pins designed for specific products can accommodate the unique flow properties and densities of different materials. This customization reduces fill variation and ensures that each capsule is filled accurately. Specialized tooling also minimizes the risk of cross-contamination between products and enhances the machine's efficiency by reducing downtime associated with tool changes and adjustments. Investing in customized tooling for different products ultimately leads to higher quality capsules and more efficient production processes.
Filling accuracy in capsule filling machines is influenced by the product's characteristics and shape. Adjustments to machine settings, such as fill weight and encapsulation parameters, are necessary to cater to different products. Proper calibration, using the right tooling, and continuous monitoring are key to achieving precise and consistent filling.
If you're looking to optimize your capsule filling process and ensure high filling accuracy for diverse products, contact us today. We offer expert consultation and a range of capsule filling machines designed to meet your specific needs. Enjoy a special discount on your first purchase and enhance your production efficiency with our advanced solutions.