Bottling filling machines are essential for maintaining efficiency and precision in production lines, whether you're dealing with pharmaceuticals, food and beverages, or cosmetics. However, like any complex machinery, they can encounter problems that might disrupt operations. Addressing these issues promptly is crucial to avoid downtime and costly repairs. In this article, we'll walk through some of the most common problems in bottling filling machines and provide practical solutions to handle them.
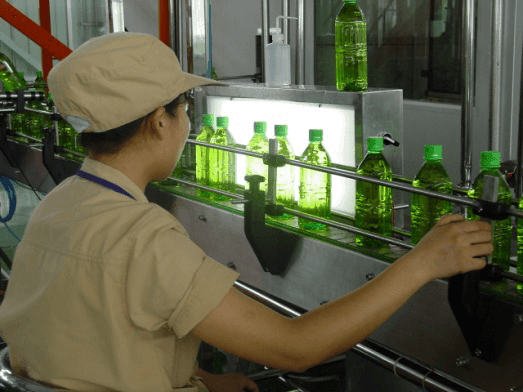
Bottle Jamming and Misalignment
Causes of Jamming:
· Incorrect machine setup or improper bottle handling: If the machine is not properly aligned or if bottles are not handled correctly, they can become misaligned or jam within the system. Misaligned bottles may block the flow of product, disrupt the filling process, and cause bottlenecks.
· Excessive dust or residue in the system: In some industries, especially food and beverage, dust or product residue can build up and cause parts of the filling system to become clogged, resulting in jams.
Solutions:
· Regular machine inspections and alignment checks: To prevent jams, it’s essential to regularly inspect and clean your bottling filling machine. Alignment checks are crucial, especially after adjustments or during routine maintenance.
· Advanced sensors to detect misalignment early: Many modern bottling machines come equipped with sensors that can detect when bottles are misaligned or jammed, helping to address the problem before it causes major disruptions. These sensors automatically stop the machine or alert operators when something goes wrong.
By regularly monitoring and inspecting the equipment, you can avoid production delays caused by bottle jams, ensuring a smooth bottling process.
Clogging in Filling Nozzles
Types o
f Clogs:
· Material build-up from sticky or high-viscosity liquids: Filling sticky substances like syrups, oils, or high-viscosity gels can cause clogging in nozzles. These materials can build up over time, causing the flow to become uneven or completely blocked.
· Particle contamination in food or beverage filling: Tiny particles of ingredients or contaminants can get lodged in the nozzles, causing clogging that impedes the filling process.
Preventive Maintenance:
· Frequent nozzle cleaning and proper filtration systems: Regular cleaning of nozzles helps to prevent the accumulation of residue and particles. Use dedicated cleaning solutions to remove buildup and keep the nozzles in top condition.
· Using self-cleaning nozzles in some applications: Some bottling machines come with self-cleaning nozzles, which can help prevent clogs by cleaning the nozzles automatically after each filling cycle.
By incorporating proper cleaning practices and filtration systems, you can minimize the risk of clogging, which helps maintain a continuous and efficient production flow.
Inconsistent Filling Volumes
Potential Caus
es:
· Pressure or temperature fluctuations: Variations in temperature or pressure can impact the consistency of the filling process. Liquids, for example, can expand or contract depending on their temperature, leading to inconsistent fills.
· Calibration issues or faulty sensors: Over time, sensors and fill volume measurement systems may become miscalibrated, leading to inaccurate filling levels.
Troubleshooting:
· Adjusting the pressure or speed to match the liquid’s viscosity: For liquids, it's essential to adjust the filling speed and pressure based on the product’s viscosity. Thicker liquids require slower filling speeds to ensure accuracy, while thinner liquids may need higher speeds.
· Regular calibration of sensors and nozzles: To ensure consistent filling, schedule routine calibrations for both sensors and filling nozzles. By maintaining these components, you can ensure that the machine dispenses the correct volume every time.
Consistent filling volumes are crucial for product quality and customer satisfaction, so addressing any inconsistencies quickly can help you avoid compliance issues and reduce waste.
Leakage or Spillage
Causes of Leakage:
· Damaged seals or improperly aligned filling heads: If seals become worn or damaged, they may fail to contain the product, leading to leakage. Additionally, filling heads that are misaligned with the bottles can cause spills during the filling process.
· Excessive product flow or inconsistent bottle handling: If the product flows too quickly or bottles are mishandled, it can lead to spillage. Bottles that are not placed correctly may overflow, creating a mess on the production line.
Solutions:
· Regular inspection of seals and gaskets: Inspect seals and gaskets frequently to ensure they are intact. Replace damaged seals to prevent leaks. Choose high-quality sealing materials to ensure longevity and durability.
· Adjusting the filling speed to prevent spillage: It’s important to control the speed at which the machine fills bottles. Too fast a filling process can cause the product to spill over, especially with liquids. Slowing the filling process down slightly can prevent this issue.
By keeping seals in good condition and adjusting the filling process as needed, you can minimize the chances of leaks and spills, improving the overall cleanliness and efficiency of the production line.
Dealing with common bottling filling machine problems can be a headache, but with the right approach and a good maintenance routine, these challenges can be easily managed. Regular inspections, prompt calibration, and routine cleaning are key to keeping your bottling line running efficiently. By addressing issues like jamming, clogging, inconsistent fills, and leakage early, you can ensure that your production processes stay smooth and that your customers receive high-quality, reliable products.