In the realm of pharmaceutical manufacturing, the precision of capsule filling machines is paramount. This article delves into the intricacies of handling filling errors and deviations during production, pinpointing the root causes, specific workstations affected, and the precise operational steps for adjustment and prevention.
Filling errors and deviations in capsule filling machines can arise from various factors, such as nozzle blockages, sensor malfunctions, or incorrect machine settings. Specific workstations, including fill volume adjustments and sensor calibration, play a crucial role in rectifying these issues. By implementing manual interventions and leveraging automatic adjustment functions, operators can effectively address and prevent filling errors, ensuring consistent production quality.
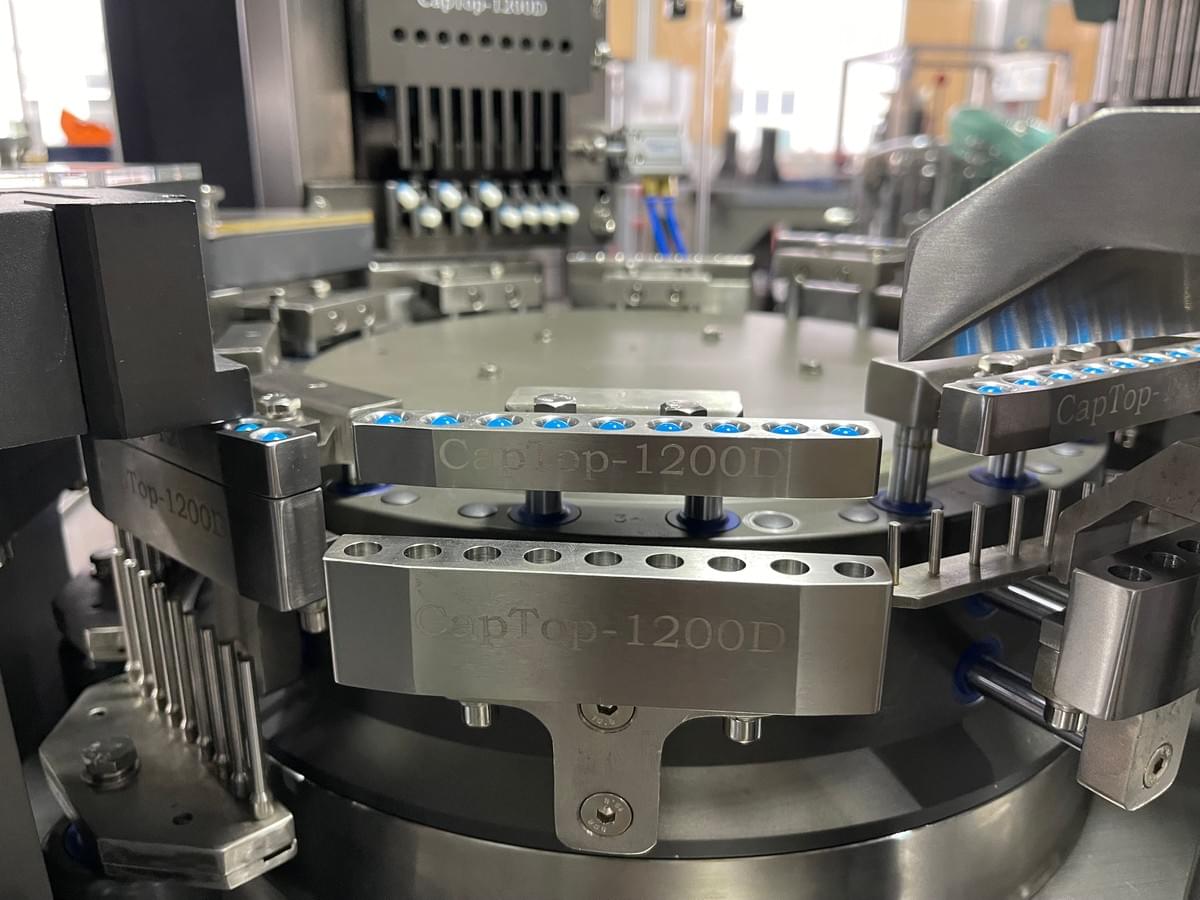
Understanding the scenarios in which filling errors and deviations occur is pivotal for effective management. Here's a detailed breakdown of the common causes and corresponding operational procedures:
Underfilled or Overfilled Capsules: These errors often stem from incorrect fill volume settings at the filling station. Operators should promptly adjust the fill volume settings through the machine's control interface to rectify the issue.
Nozzle Blockages: Blockages in the filling nozzles disrupt the flow of powder or granules, leading to inconsistent fill volumes. Operators must inspect and clear nozzle blockages regularly using appropriate cleaning tools to ensure smooth operation.
Sensor Malfunctions: Inaccuracies in fill volume readings may result from sensor malfunctions or misalignments. Operators should conduct regular sensor calibrations and adjustments to maintain accurate measurements, as outlined in the machine's manual.
Routine Maintenance: Preventive maintenance is crucial for averting filling errors and deviations. Operators should adhere to a comprehensive maintenance schedule, including lubrication, inspection of moving parts, and replacement of worn components, to uphold machine performance and reliability.
While manual interventions are indispensable for addressing filling errors during production, automatic adjustment functions offer a proactive approach to maintaining accuracy. The subsequent sections will explore the integration of automatic adjustment functions and their role in mitigating filling errors and deviations.
Can the Filling Accuracy Be Customized and Adjusted According to Production Needs? How to Achieve?
Yes, filling accuracy can be tailored to specific production requirements through manual adjustments or automatic adjustment functions, such as fill volume calibration and sensor recalibration.
How to Balance the Relationship Between Filling Accuracy and Production Speed?
Achieving an optimal balance between filling accuracy and production speed entails fine-tuning machine settings and operational parameters. Operators should prioritize quality control measures while maximizing throughput to meet production demands.
Is the Precision Control During the Filling Process Affected by Environmental Factors? How to Deal with the Impact of Environmental Changes on Accuracy?
Environmental fluctuations, such as temperature and humidity, can influence precision control during the filling process. Implementing environmental controls and regular calibration procedures helps mitigate these effects on filling accuracy.
Is There a Dedicated Filling Accuracy Monitoring System for Real-Time Detection and Adjustment?
Many modern filling machines feature dedicated monitoring systems for real-time detection, adjustment, and data recording to optimize quality control processes and ensure consistent filling accuracy.
Is filling accuracy affected by operator skill level? How to ensure operator training and operational standardization?
Operator training and standardization are critical for maintaining consistent filling accuracy. Robust training programs and adherence to standard operating procedures foster operator competency and operational standardization.
In the realm of pharmaceutical manufacturing, addressing filling errors and deviations is imperative for ensuring product quality and regulatory compliance. By identifying the root causes, leveraging manual interventions and automatic adjustment functions, and prioritizing preventive maintenance, operators can effectively mitigate filling errors and deviations, ensuring reliable production outcomes.
Looking to optimize your capsule filling processes and safeguard against filling errors and deviations? Contact us today to explore our advanced capsule filling machines equipped with manual intervention capabilities and automatic adjustment functions. Our team stands ready to provide guidance on operational procedures, preventive maintenance, and machine integration to meet your production needs with precision and efficiency.