In the process of medicine and other industrial production, mixer is a common equipment. Its function is to mix two or more materials evenly. In recent years, with the rapid development of pharmaceutical industry, mixer equipment also ushered in the objective market prospects. At present, three-dimensional mixer and two-dimensional mixer are common in the market.
The two-dimensional mixer moves in x-axis and Y-axis directions, which is the multi-directional movement of mixing cylinder. The material has no centrifugal force, no specific gravity segregation, stratification and accumulation phenomenon. The weight ratio of each component can be very different, and the mixing rate is more than 99.9%. It has the advantages of good mixing effect and efficiency, large cylinder loading rate and short mixing time. It is suitable for high uniformity mixing of powdery and granular materials in pharmaceutical, chemical, food, light industry, electronics, machinery, mining and metallurgy industries.
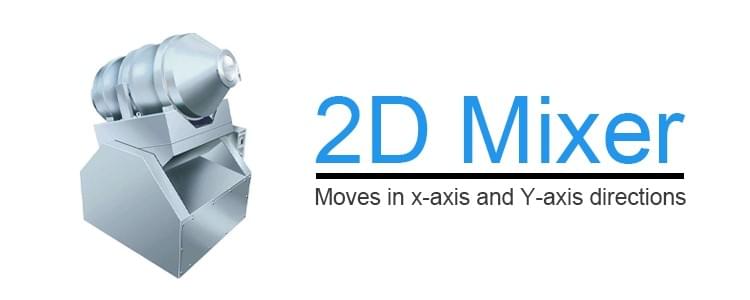
The three-dimensional mixer is moving in three XYZ axes, and the materials in the cylinder can be fully mixed through the mixing cylinder which is rotating and swinging at the same time. It is widely used in medicine, chemical industry, food, feed, pesticide and other industries, especially for the mixing of large tonnage solid materials.
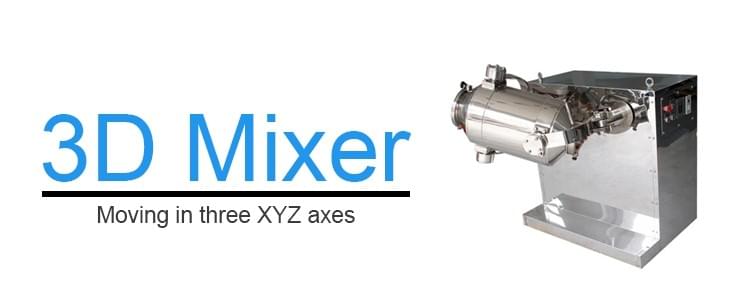
There are some differences between the two kinds of mixers, but no matter which kind of mixer, if the user wants the mixing effect of materials to reach the ideal state, the machine and equipment must be selected correctly. So, how to select the mixer? In this regard, some blender manufacturers made a brief selection skills to share.
First, in addition to the structural strength and power of the mixer, there are also large differences in the structural methods of the discharge gate, rotor, body, and even the performance parameters such as speed. Therefore, if the specific gravity of materials is different, it can not be regarded as local reinforcement or power scaling.
Second, if the particle size of the material is fine, special attention should be paid to whether the sealing performance of the mixer is good or not, and also pay attention to its residual amount. If possible, the user can choose the upper cloth bag to exhaust air instead of the return air pipe, so as to avoid excessive fine flour from the outlet of the return air pipe when mixing.
Third, users should consider the influence of other factors on the purchase of equipment. If it is necessary to clean the equipment due to material bonding, the user should select the cleaning door with automatic cleaning device; if the material with high requirements for particle integrity, it is suitable to select the rotary type container equipment.
Fourth, if it is a mixture of materials that need to be heated or accompanied by chemical reactions, users should not only consider the material and structure of the machine, but also consider the influence of temperature change on the whole machine. At the same time, the corresponding methods should be adopted in the design of the main shaft and rotor of the equipment.
Fourth, in general, the installation space is also a problem that users often need to consider when choosing hybrid. Of course, in addition to its own device size, reasonable site layout and installation method can also effectively improve the installation space conditions.
Generally speaking, the selection of mixer looks simple, but in fact it needs skills. If the selection is not correct, the user may have problems in the process of operation, affect the production schedule, and waste the cost of the enterprise and cause irreparable losses. Therefore, users should pay attention to the process of equipment selection and understand the selection skills, so as to make a better purchase judgment and find the equipment suitable for the actual production needs.