Ever wondered how those tiny, perfectly shaped tablets you see in medicine bottles are made? Tablet presses are the unsung heroes of the pharmaceutical and nutraceutical industries, turning powdered ingredients into uniform tablets with precision and efficiency. In this guide, we’ll walk you through the fascinating process of how a tablet press works, breaking down each step so you can get a clear picture of what happens behind the scenes.
A tablet press takes powder and transforms it into tablets through a series of steps like filling, metering, compression, and ejection. It’s a carefully controlled process designed to ensure each tablet is just right.
Tablet Press Operation Stages
1. Filling
Imagine a funnel, but a bit more sophisticated. The powder flows from a hopper into the die cavity, where the magic begins. The lower punch is ready to catch the powder, and the feed frame ensures the powder is evenly spread. No overfilling, no mess—just the right amount of powder in each cavity.
2. Metering
This is where precision really comes into play. The machine measures out exactly the right amount of powder, making sure each tablet will weigh the same and contain the right dose. Any extra powder? It’s whisked away to keep everything neat and tidy.
3. Compression
This step is a two-part process:
- Pre-compression: The upper punch comes down gently, giving the powder a little squeeze to form a loose tablet called a slug. This helps get rid of any air pockets that could mess with the tablet’s quality.
- Main Compression: Now for the real squeeze! The upper punch comes down with more force, turning that slug into a finished tablet with just the right hardness and thickness.
4. Ejection
Finally, the lower punch pushes the tablet up and out of the die cavity. Thanks to some handy lubricants, the tablet slides out smoothly, ready to be packaged and sent off.
Want more details? Visit our Tablet Press Overview page for an in-depth look.
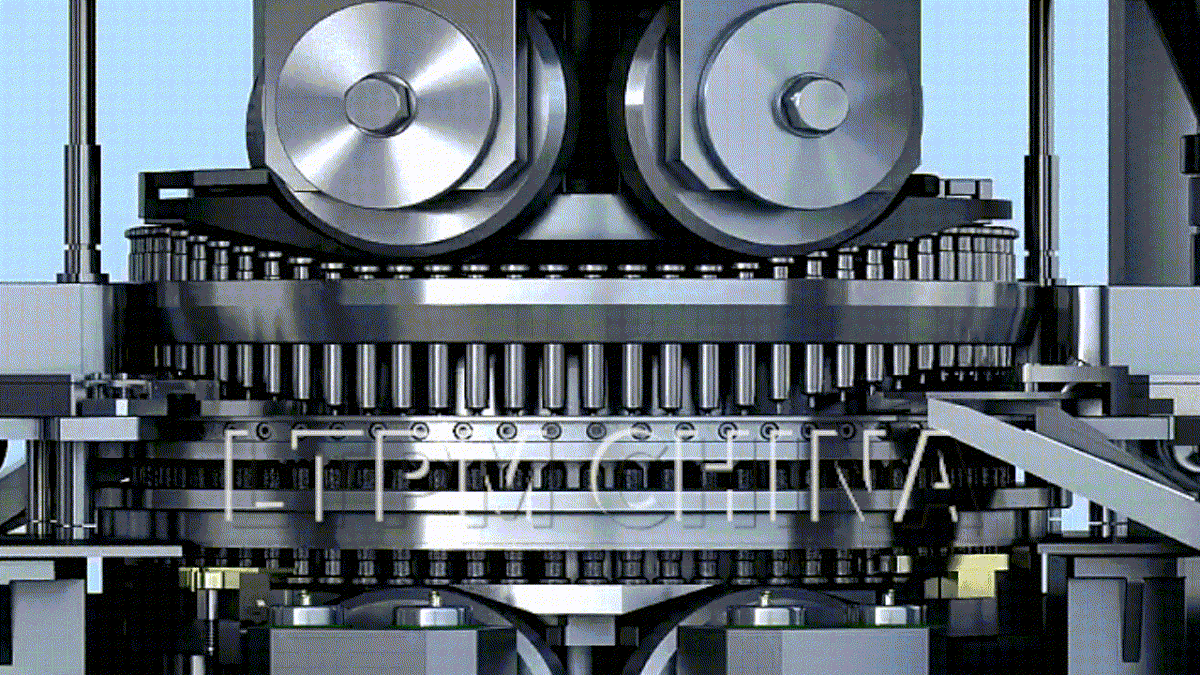
Types of Tablet Presses
Tablet presses come in different shapes and sizes, depending on the production scale:
- Single Punch Tablet Press: Ideal for smaller batches, this press uses one punch and die set. It’s simple, but it gets the job done. Learn more on our Single Punch Tablet Press page.
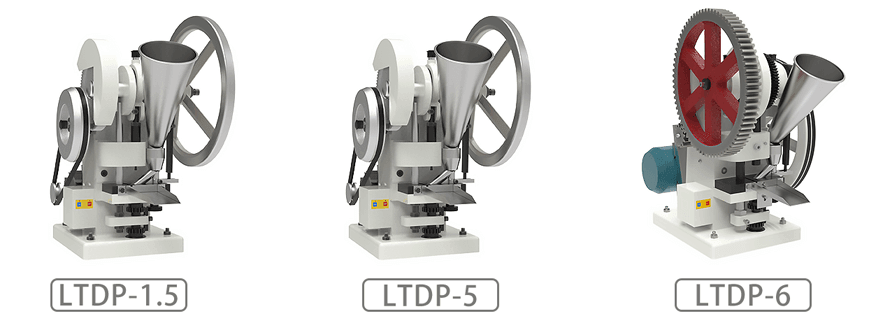
- Rotary Tablet Press: For when you need to go big. This machine has a rotating turret with multiple punch and die sets, perfect for large-scale, continuous production. Find out more on our Rotary Tablet Press page.
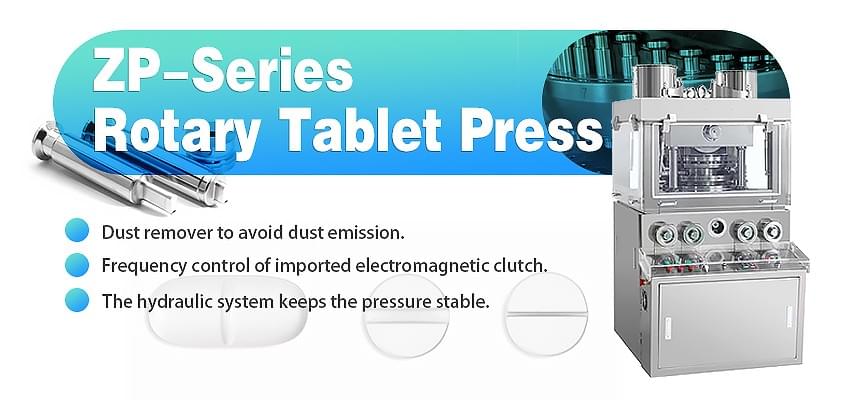
Key Components of a Tablet Press
Here’s a quick rundown of the main parts:
- Hopper: Holds the powder before it’s fed into the machine.
- Feeder: Spreads the powder into the die cavity.
- Die Cavity: The mold that shapes the tablet.
- Punches: The upper and lower punches compress the powder to form the tablet.
Adapting Tablet Presses for Different Tablet Types
Different types of tablets, such as shaped tablets, sustained-release tablets, and multi-layer tablets, require specific adjustments and techniques in the tablet press operation:
1. Shaped Tablets
- Die and Punch Design: Specially designed punches and dies create tablets with specific shapes. The design must ensure uniform compression and avoid defects like chipping or capping.
- Compression Settings: Adjustments in compression force and dwell time are crucial to maintaining the integrity of shaped tablets.
2. Sustained-Release Tablets
- Granulation: The granulation process includes polymers or other agents that control the release rate of the active ingredient.
- Compression Stages: Ensuring even distribution of these agents throughout the tablet is crucial, requiring precise compression settings.
3. Multi-Layer Tablets (e.g., Bi-Layer, Tri-Layer)
- Layering Process: Involves sequential filling and compression stages for each layer. The first layer is filled and lightly compressed, followed by subsequent layers.
- Synchronization: The tablet press must synchronize each layer to adhere properly without mixing or delamination.
- Compression Force: Adjusting the compression force for each layer prevents cross-contamination and ensures tablet integrity.
Related Topics and FAQs
What Affects Tablet Quality?
Tablet quality hinges on factors like granulation, compression force, and the design of the tooling. Ensuring uniform granulation and precise compression helps produce high-quality tablets every time.
What’s New in Tablet Press Technology?
From automation to real-time monitoring, the latest tech makes tablet production faster, more efficient, and more reliable, ensuring compliance with industry standards.
What Are the Regulatory Standards?
Strict regulations from bodies like the FDA and EMA ensure that tablets are safe and effective. Compliance involves rigorous process validation, equipment calibration, and meticulous documentation.
How Is Material Handling Managed?
Proper handling of raw materials is key to preventing contamination and ensuring consistent quality. Automated systems can help by accurately measuring and delivering materials to the tablet press.
How to Troubleshoot Common Issues?
Issues like weight variation, sticking, or capping can often be solved by adjusting compression settings, using anti-adherent coatings, or ensuring proper machine maintenance.
Tablet presses are essential tools in the pharmaceutical world, ensuring that each tablet is consistent in quality and dosage. By understanding how these machines work and how to adjust them for different tablet types, manufacturers can produce top-quality products efficiently. Keeping up with the latest technology and regular maintenance are the keys to smooth and successful tablet production.
Need expert advice on optimizing your tablet production process? Reach out to us at Zhejiang Leadtop Pharmaceutical Machinery Co., Ltd. We’re here to help! Visit our Tablet Press Overview, Rotary Tablet Press, and Single Punch Tablet Press pages to learn more.