In many drying equipment, spray dryer is one of the widely used drying equipment. Spray dryer is a drying equipment for treating solution, suspension or slurry material. It can be directly dried from liquid to powder, which is the biggest advantage of spray dryer. Its low thermal efficiency, large volume, low production capacity and high investment are its shortcomings. Spray drying machine is widely used in chemical industry, light industry and food industry because it can be directly obtained from solution or suspension system with uniform powder products. Chemical industry is widely used in dyestuff industry.
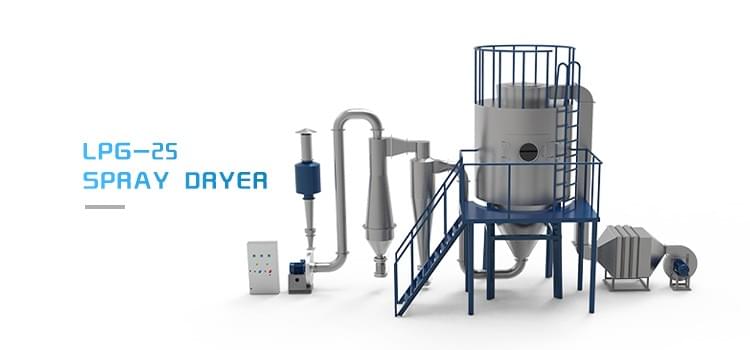
The principle of spray dryer is to spray the material into droplets and disperse them in hot air by spray method. The material is contacted with the hot air in the way of parallel flow, countercurrent or mixed flow, so that the moisture evaporates quickly and achieves the purpose of drying.
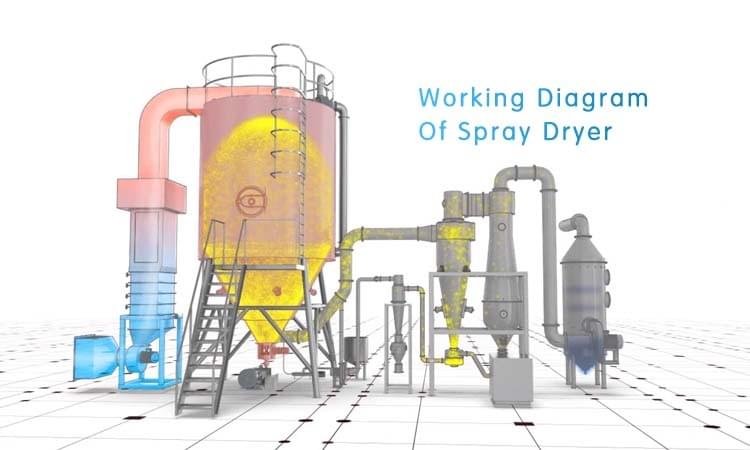
The nozzle of the spray dryer is a precision device which can promote the dispersion of liquid into the spray. The nozzle is used for three purposes: to distribute the liquid over an area, to increase the surface area of the liquid, and to produce an impact force on the solid surface. All kinds of nozzle applications use various spray characteristics to describe spray.
The nozzle of the spray dryer can be classified according to the energy input for atomization, and the fluid can be decomposed into droplets. A nozzle may have one or more outlets; a multiple outlet nozzle is called a composite nozzle. The nozzle ranges from heavy industrial use to light spray cans or spray bottles.
The ultrasonic nozzle is another nozzle used on the pressure spray dryer. The high-frequency vibration generated by piezoelectric sensor acts on the tip of the nozzle, resulting in capillary waves in the liquid film. Once the amplitude of the capillary waves reaches a critical height (due to the power level provided by the generator), they become too high to support themselves, and there are tiny droplets at the tip of each wave, causing atomization.
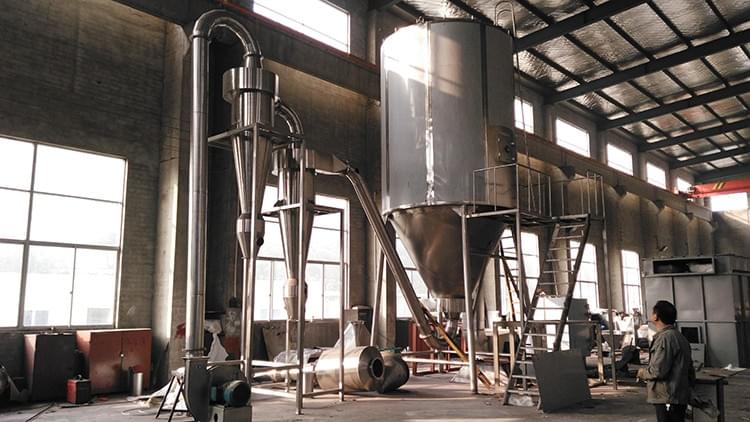
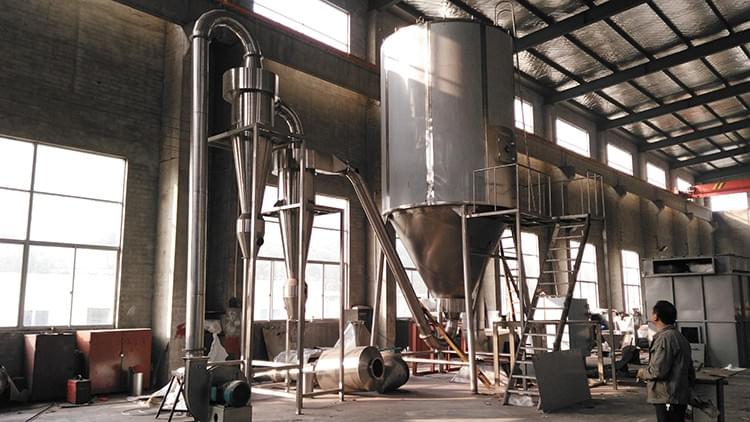
In designing centrifugal spray dryer, we must determine the size and distribution of dry particles in advance. Because these two factors will directly affect the bulk density and color of dried products. Therefore, only asuitable centrifugal spray dryer can be selected to achieve a good drying effect.
What are the factors that need to be considered in designing centrifugal spray dryer? The so-called bulk density is actually the bulk density, which is generally determined before the design. There are four factors that affect bulk density, which are equipment type, hot air and exhaust temperature, feed concentration and additives.
First of all, if the type of equipment selected is different, what will be the impact? In terms of usage, if the combined flow centrifugal spray dryer is chosen, a product with a smaller density will be obtained; if the countercurrent centrifugal spray dryer is used, a product with greater density will be obtained.
Therefore, when choosing, the type of spray dryer should be determined according to the actual production requirements. Secondly, in the process of feeding, we should also pay attention to the control of the feed concentration. This is because, in the course of the centrifugal spray dryer, generally speaking, the feed concentration is directly proportional to the bulk density. If the feed concentration is low, the bulk density will be small. If the feed concentration is high, then the bulk density will be large.