Capsule filling machines are integral to pharmaceutical manufacturing, requiring efficient maintenance and occasional upgrades to ensure optimal performance. Understanding whether these machines feature a modular design can greatly impact decision-making for pharmaceutical buyers and manufacturers.
Yes, many modern capsule filling machines incorporate a modular design in their mechanical structure to facilitate maintenance and upgrades. Modular components allow for easier access, troubleshooting, and replacement, ultimately reducing downtime and enhancing overall efficiency in pharmaceutical production facilities.
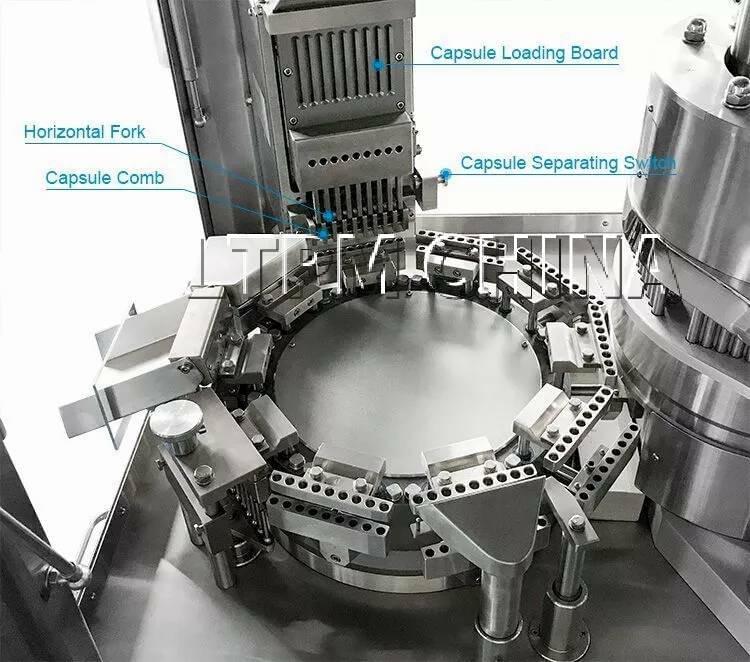
1. Modular Components:
Modular design involves breaking down the mechanical structure of the capsule filling machine into interchangeable modules or parts. These modular components can be easily accessed, removed, and replaced without requiring extensive disassembly of the entire machine. Common modular components include filling nozzles, dosing discs, turret segments, and sealing stations.
2. Ease of Maintenance:
The modular design of capsule filling machines simplifies maintenance tasks by allowing operators to focus on specific components without affecting the overall functionality of the machine. Routine maintenance, such as lubrication, cleaning, and inspection, can be performed more efficiently, reducing the time and resources required for upkeep.
3. Accessibility and Troubleshooting:
Modular components are designed to be easily accessible, making it easier for operators to diagnose and troubleshoot issues that may arise during operation. With clear access points and standardized interfaces, technicians can quickly identify faulty components and implement corrective actions to minimize downtime and maintain productivity.
4. Flexibility and Scalability:
The modular nature of capsule filling machines offers flexibility and scalability for pharmaceutical manufacturers. Upgrades or modifications can be implemented by simply replacing or adding modular components, rather than investing in entirely new equipment. This flexibility allows manufacturers to adapt to changing production requirements and technologies without significant capital investment.
5. Compatibility and Interchangeability:
Modular components are often designed to be compatible and interchangeable across different machine models and manufacturers. This interoperability streamlines procurement processes and reduces reliance on proprietary parts, giving manufacturers more options for sourcing components and reducing maintenance costs over time.
Understanding the benefits of a modular design in the mechanical structure of capsule filling machines can significantly impact decision-making for pharmaceutical buyers and manufacturers. Now, let's explore related topics to gain further insights into maintenance practices, upgrades, and the overall efficiency of capsule filling operations.
What are the key considerations when selecting a capsule filling machine with a modular design, and how does modularity impact long-term maintenance costs?
Key considerations include the availability of modular components, ease of access, compatibility with existing equipment, and support from manufacturers for upgrades and replacements. Modularity can reduce long-term maintenance costs by simplifying upkeep and minimizing downtime associated with repairs and upgrades.
How do manufacturers ensure the compatibility and interchangeability of modular components across different machine models and brands?
Manufacturers often adhere to industry standards and design guidelines to ensure the compatibility and interchangeability of modular components. Additionally, collaborative efforts among industry stakeholders may lead to the development of standardized interfaces and interoperable components, further enhancing compatibility.
What role does predictive maintenance play in maximizing the efficiency of capsule filling machines with modular designs, and how can manufacturers implement predictive maintenance strategies effectively?
Predictive maintenance leverages data analytics and sensor technology to anticipate equipment failures and schedule maintenance activities proactively. Manufacturers can implement predictive maintenance strategies effectively by integrating condition monitoring systems, collecting and analyzing performance data, and leveraging predictive analytics to forecast maintenance needs.
How can operators optimize the performance of capsule filling machines through regular maintenance practices, and what are some common maintenance challenges they may encounter?
Operators can optimize machine performance by adhering to manufacturer-recommended maintenance schedules, conducting routine inspections, and promptly addressing any issues that arise. Common maintenance challenges include identifying and sourcing replacement parts, coordinating maintenance activities, and ensuring compliance with regulatory requirements.
What are the potential risks and drawbacks associated with modular designs in capsule filling machines, and how can manufacturers mitigate these risks effectively?
Potential risks include increased complexity, compatibility issues, and the risk of component failure. Manufacturers can mitigate these risks by conducting thorough risk assessments, designing robust modular components, providing comprehensive training for operators, and offering responsive technical support and maintenance services.
The modular design of capsule filling machines offers numerous benefits, including ease of maintenance, accessibility, flexibility, and compatibility. By leveraging modular components, pharmaceutical manufacturers can streamline maintenance tasks, facilitate upgrades, and enhance overall efficiency in capsule filling operations.
Ready to explore capsule filling machines with modular designs to streamline maintenance and enhance efficiency in your pharmaceutical production facility? Contact us today to learn more about our innovative equipment solutions and discuss your specific requirements. Plus, inquire about our special offers and financing options to optimize your capsule filling operations and stay ahead in the competitive pharmaceutical market.