In pharmaceutical manufacturing, downtime can be costly and disruptive. Capsule filling machines are essential for efficient production, but how does the filling volume adjustment process impact downtime? This article explores whether shutting down the machine is necessary during volume adjustments and offers practical strategies to minimize downtime in capsule filling operations.
The filling volume adjustment process in capsule filling machines typically does not require a complete shutdown. Modern machines are equipped with advanced features that allow for real-time adjustments without interrupting production. By implementing proactive maintenance and utilizing machine capabilities effectively, downtime during volume adjustments can be minimized.
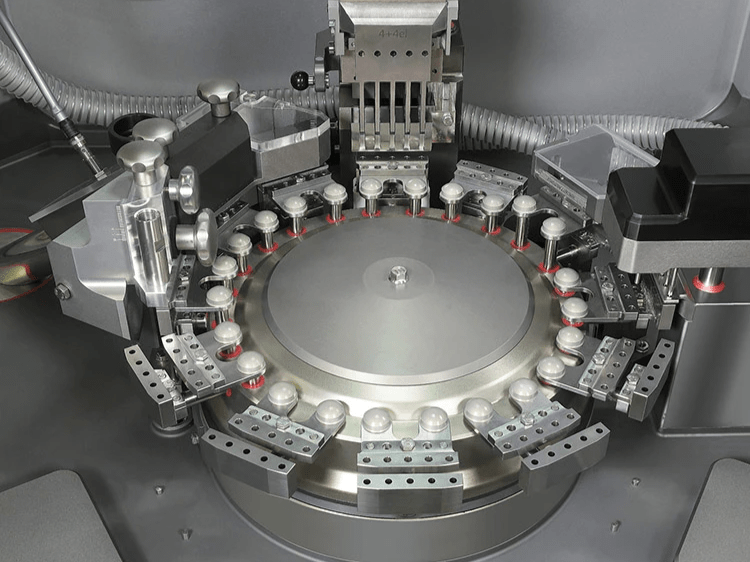
Capsule filling machines are designed for continuous operation, and the volume adjustment process is no exception. Here's how manufacturers can ensure minimal downtime:
Dynamic Adjustment Controls: Many capsule filling machines feature dynamic adjustment controls, enabling operators to make real-time changes to filling volumes without stopping the machine. These controls streamline the adjustment process and minimize downtime associated with volume changes.
Remote Monitoring and Control: Advanced capsule filling machines offer remote monitoring and control capabilities, allowing operators to adjust filling volumes from a central control panel. This eliminates the need for manual intervention and reduces downtime during volume adjustments.
Predictive Maintenance: Implementing predictive maintenance practices helps identify potential issues before they cause downtime. Regular inspections, proactive repairs, and equipment upgrades ensure that capsule filling machines operate smoothly, minimizing the risk of unexpected shutdowns.
Understanding the impact of the filling volume adjustment process on downtime is crucial for optimizing productivity in capsule filling operations. The following section will delve into additional strategies for minimizing downtime and maximizing efficiency in capsule filling processes.
How to Detect and Verify Filling Accuracy? Is There an Automated Detection System?
Many modern capsule filling machines are equipped with automated detection systems, such as weight sensors or vision inspection systems, to ensure filling accuracy. These systems detect deviations from the desired fill volume and trigger corrective actions, ensuring product quality and consistency.
How to Deal with Filling Errors and Deviations During Production? Is There an Automatic Adjustment Function?
Capsule filling machines often feature automatic adjustment functions that correct filling errors and deviations in real-time. These functions minimize product waste and ensure that each capsule meets quality standards without manual intervention.
Can the Filling Accuracy Be Customized and Adjusted According to Production Needs? How to Achieve?
Yes, filling accuracy can be customized and adjusted according to production needs by configuring machine settings and parameters. Operators can adjust fill volumes, speeds, and other parameters to meet specific product requirements and optimize production efficiency.
How to Balance the Relationship Between Filling Accuracy and Production Speed?
Achieving a balance between filling accuracy and production speed requires careful optimization of machine settings and parameters. Manufacturers can fine-tune fill volumes and speeds to maximize throughput while maintaining consistent fill weights and product quality.
Is the Precision Control During the Filling Process Affected by Environmental Factors? How to Deal with the Impact of Environmental Changes on Accuracy?
Environmental factors such as temperature and humidity can affect the precision control of capsule filling machines. Implementing environmental controls, such as climate-controlled production facilities, helps minimize the impact of these factors on filling accuracy and ensure consistent performance.
Efficient operation of capsule filling machines is crucial for pharmaceutical manufacturers to meet production targets and minimize downtime. By understanding the impact of the filling volume adjustment process on downtime and implementing proactive strategies to minimize disruptions, manufacturers can optimize productivity and ensure consistent product quality.
Are you seeking solutions to optimize the efficiency and productivity of your capsule filling operations? Contact us today to explore our expertise in capsule filling machine technology and customized solutions tailored to your specific needs. Benefit from our comprehensive support and enhance the performance of your pharmaceutical manufacturing processes.