In today's rapidly evolving manufacturing landscape, how can pharmaceutical companies optimize their production processes while minimizing energy consumption? Let's delve into the intricacies of mechanical structure design, focusing on capsule filling machines, to explore how manufacturers can strike a balance between production efficiency and energy conservation.
Yes, the design of mechanical structures, including capsule filling machines, must consider both production efficiency and energy consumption. This balance is essential for pharmaceutical manufacturers to meet production demands while minimizing operational costs and environmental impact.
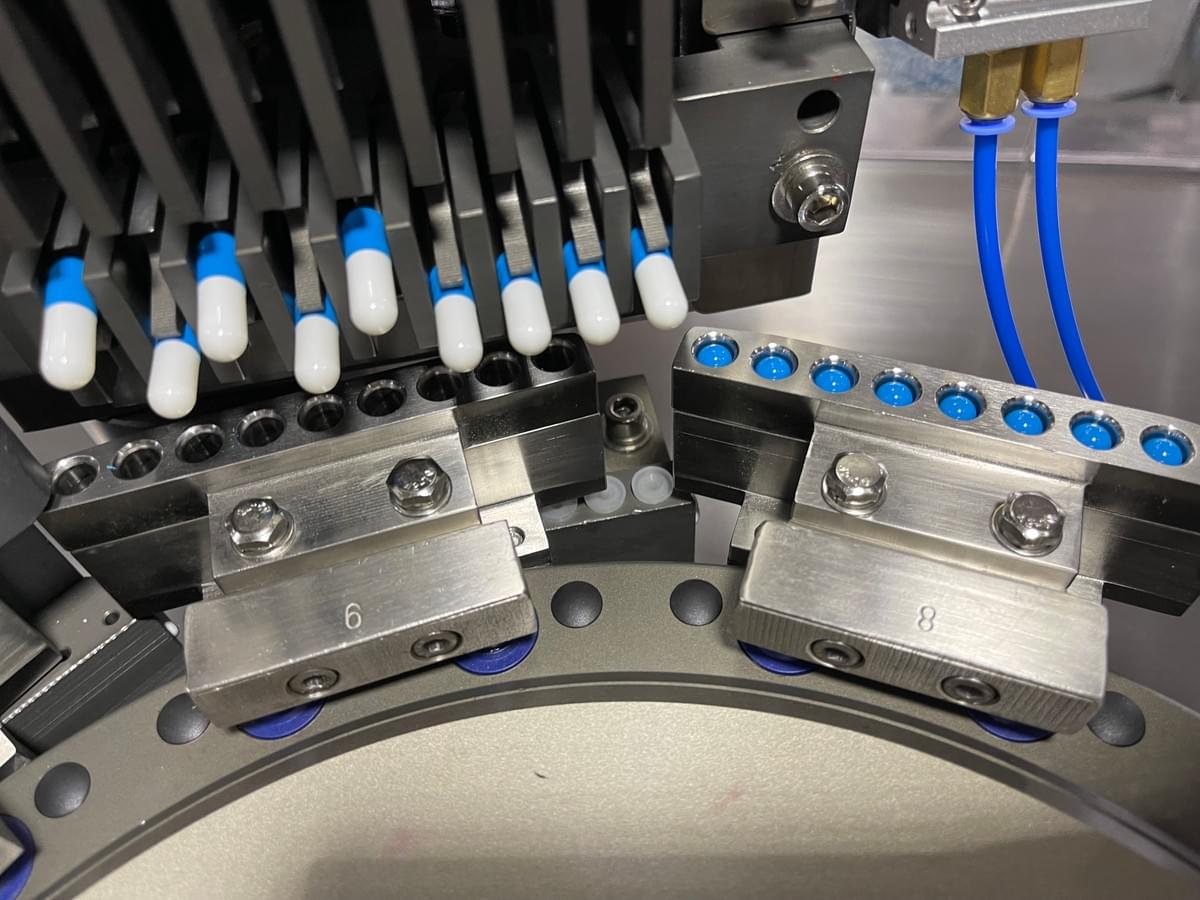
Mechanical structure design in pharmaceutical machinery encompasses various elements, from material selection to component layout and automation features. Each aspect plays a vital role in determining the overall performance and sustainability of the equipment.
Material Selection: The choice of materials for constructing mechanical structures greatly influences both production efficiency and energy consumption. Lightweight yet durable materials, such as aluminum alloys or advanced composites, can reduce the energy required for machine operation while enhancing maneuverability and speed. Additionally, materials with high thermal conductivity facilitate heat dissipation, preventing overheating and minimizing energy loss during prolonged use.
Component Integration: Efficient mechanical structure design involves seamless integration of components to optimize workflow and minimize energy waste. Capsule filling machines, for instance, require precise coordination between dosing units, tamping mechanisms, and capsule handling systems. By strategically positioning these components and streamlining their interactions, manufacturers can improve overall equipment efficiency (OEE) and reduce energy consumption.
Automation and Control Systems: Incorporating advanced automation and control systems is essential for enhancing production efficiency and reducing energy overhead. Modern capsule filling machines feature programmable logic controllers (PLCs) and sensor-based technologies that enable real-time monitoring and adjustment of operating parameters. By automating repetitive tasks and optimizing process parameters, manufacturers can achieve higher throughput rates while minimizing energy usage and material wastage.
Energy-Efficient Operation Modes: Mechanical structures can be designed to incorporate energy-efficient operation modes, such as variable frequency drives (VFDs) and regenerative braking systems. These technologies allow equipment to adjust power consumption based on workload demands, reducing energy spikes during peak production periods and conserving resources during idle or low-demand phases.
Lifecycle Analysis and Sustainability: Beyond initial design considerations, manufacturers must also conduct lifecycle assessments to evaluate the long-term environmental impact of mechanical structures. Sustainable design practices, such as modular construction, recyclable materials, and energy-efficient upgrades, can significantly reduce the carbon footprint of pharmaceutical machinery throughout its operational lifespan.
Having explored the fundamentals of mechanical structure design for capsule filling machines, let us now delve into related topics to gain a comprehensive understanding of production efficiency and energy conservation in pharmaceutical manufacturing.
How can pharmaceutical manufacturers streamline production processes to maximize efficiency and minimize energy consumption?
Efficient production workflow optimization involves careful analysis of each manufacturing step to identify inefficiencies and bottlenecks. By implementing lean manufacturing principles and workflow automation, pharmaceutical companies can minimize idle time and energy waste while improving overall productivity. Integrating advanced technologies such as robotics and artificial intelligence (AI) can further enhance efficiency by enabling real-time monitoring and adaptive process control.
What are some effective strategies for monitoring and reducing energy usage in pharmaceutical facilities?
Implementing energy management systems (EMS) and conducting energy audits are critical steps in identifying areas of energy inefficiency within pharmaceutical facilities. By investing in energy-efficient equipment and implementing energy-saving practices such as equipment scheduling and load management, companies can significantly reduce their energy consumption and operational costs. Additionally, leveraging renewable energy sources such as solar or wind power can further enhance sustainability and reduce reliance on conventional energy sources.
How are advancements in materials science and automation technology driving sustainability initiatives in the pharmaceutical industry?
Advancements in materials science have led to the development of lightweight and durable materials that improve the efficiency and sustainability of mechanical structures in pharmaceutical machinery. Additionally, automation technologies such as machine learning and predictive maintenance enable proactive energy management and optimization, reducing downtime and enhancing overall equipment efficiency. By embracing these innovations, pharmaceutical manufacturers can achieve higher levels of sustainability while remaining competitive in the global market.
What regulatory frameworks and industry guidelines govern the design and operation of pharmaceutical machinery to ensure environmental sustainability?
Pharmaceutical manufacturers must adhere to stringent regulatory standards and environmental guidelines to ensure the safety and sustainability of their operations. Regulatory bodies such as the Food and Drug Administration (FDA) and the International Organization for Standardization (ISO) impose strict requirements on equipment design, maintenance, and operation to minimize environmental impact and ensure product quality. By complying with these regulations and implementing best practices in environmental management, companies can build trust with stakeholders and demonstrate their commitment to sustainability.
What are some real-world examples of companies successfully balancing production efficiency and energy conservation in pharmaceutical manufacturing?
Several pharmaceutical companies have successfully implemented innovative strategies to optimize production efficiency and reduce energy consumption. For example, Pfizer Inc. has invested in energy-efficient equipment and renewable energy sources to reduce its carbon footprint and achieve cost savings. Similarly, Novartis AG has implemented lean manufacturing principles and process automation to streamline production workflows and minimize energy waste. By studying these case studies and adopting best practices, pharmaceutical companies can learn from industry leaders and enhance their own sustainability initiatives.
In conclusion, the design of mechanical structures, particularly capsule filling machines, is integral to achieving a balance between production efficiency and energy consumption in the pharmaceutical industry. By embracing innovative technologies, implementing energy management strategies, and adhering to regulatory standards, companies can optimize their operations while minimizing environmental impact. Moving forward, a holistic approach that integrates technological innovation, regulatory compliance, and continuous improvement will be essential for driving sustainable growth and competitiveness in pharmaceutical manufacturing.