In the pharmaceutical industry, sugar coating enhances the appearance, flavor, and stability of tablets. This guide outlines the sugar coating process, from initial sealing to final polishing. The guide discusses the advantages and disadvantages of each step, as well as the differences among various coating machines.
1. Sealing
The first step in sugar coating is sealing. Sealing involves applying a thin layer to prevent interaction between the core ingredients and the sugar coating. Sealants come in various forms, including:
- Cellulose Acetate Phthalate (CAP): A polymer with excellent film-forming and moisture-resistant properties.
- Polyvinyl Acetate Phthalate (PVAP): Known for its effectiveness and stability as a moisture barrier.
- Zein: A corn protein derivative with natural origins and moisture protection capabilities.
Sealing protects the tablet core from moisture and prevents the active ingredients from interfering with the sugar coating, which could lead to tablet degradation. Shellac, an older sealant, was common but hardens over time and is no longer used. Modern sealants like CAP or PVAP are preferred for their reliability and stability. After sealing, the tablets appear slightly glossy and are protected by a clear or slightly opaque outer layer. This layer protects the tablet core from environmental factors and moisture.
Typically, each tablet uses 10-15 mg of sealant. The solvent evaporates, leaving a protective coating. The core must be strengthened, and a moisture barrier formed. The choice and application of sealant depend on the tablet's porosity. Highly porous tablets require careful application to ensure a uniform coating.
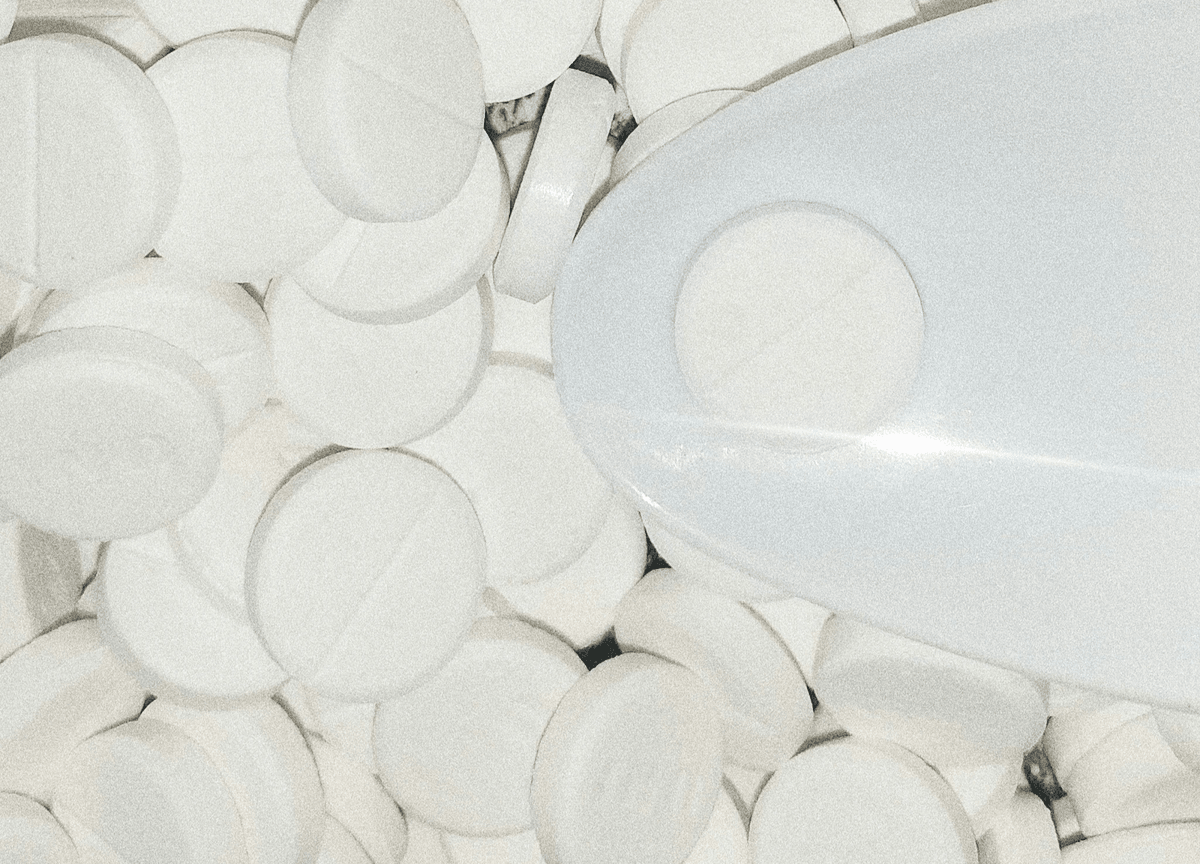
2. Subcoating
Subcoating is essential for giving the tablet a smooth, rounded shape, which increases the tablet's size. Subcoating also covers any surface imperfections. It makes the tablets look larger, more rounded, and more voluminous. The tablets appear opaque, with a thicker outer layer than the original tablet, hiding initial imperfections. Subcoating typically uses either the lamination or suspension method to apply multiple layers of syrup.
- Lamination Method: Combines binders like sucrose, acacia, and gelatin with powders like calcium carbonate or talc.
- Suspension Method: Fillers are added to a gum solution, followed by sucrose.
Lamination involves applying an adhesive and sucrose solution, then dusting with powder. This process is repeated until the desired shape and size are achieved. Subcoating is typically applied at 25-50 mg per tablet, increasing size and weight. This method ensures consistency and is more suited for automated processes.
3. Smoothing
This stage involves applying a 60-70% sugar solution to create a smooth, even surface. The smoothing stage is repeated several times (9-10 cycles), adding 5-10 mg of syrup per tablet. Smoothing prepares the tablet surface for coloring, creating a uniform, aesthetically pleasing appearance.
Many syrup solutions contain additional ingredients like gelatin or acacia to achieve a smooth finish. Repeated applications ensure any surface irregularities are corrected, resulting in a smooth surface for subsequent coloring.
Smoothing ensures the product has a uniform appearance and texture, both crucial for customer acceptance. After smoothing, the tablets have a uniform, glossy surface. With a consistent texture and smooth surface, the tablets are ready for coloring.
4. Coloring
Coloring involves using a solution of syrup and colorant. Aluminum lake pigments are used in modern processes for their uniformity and stability. Typically, the syrup concentration is 70%, and the pigment amount is 1-5%, depending on the desired shade. Careful monitoring of this stage is essential to prevent color variations and ensure uniform distribution.
Historically, water-soluble dyes caused inconsistencies and color migration. Today, aluminum lake pigments are popular for their color consistency and stability.
5. Polishing
Polishing makes the tablets glossy and professionally attractive. Common waxes include carnauba wax, beeswax, and candelilla wax. In a typical polishing pan, each tablet receives 1-2 mg of wax. After this step, the tablets look better and are protected.
6. Custom Printing
Custom printing with edible ink provides brand identification. When embossing is not feasible due to the sugar coating, edible ink is used. Tablets are easily identifiable and can be branded without damaging the sugar coating.
Printed tablets are clear and readable, including brand identification, dosage information, or any other details. This ensures the tablets are easily identifiable and meet regulatory requirements.
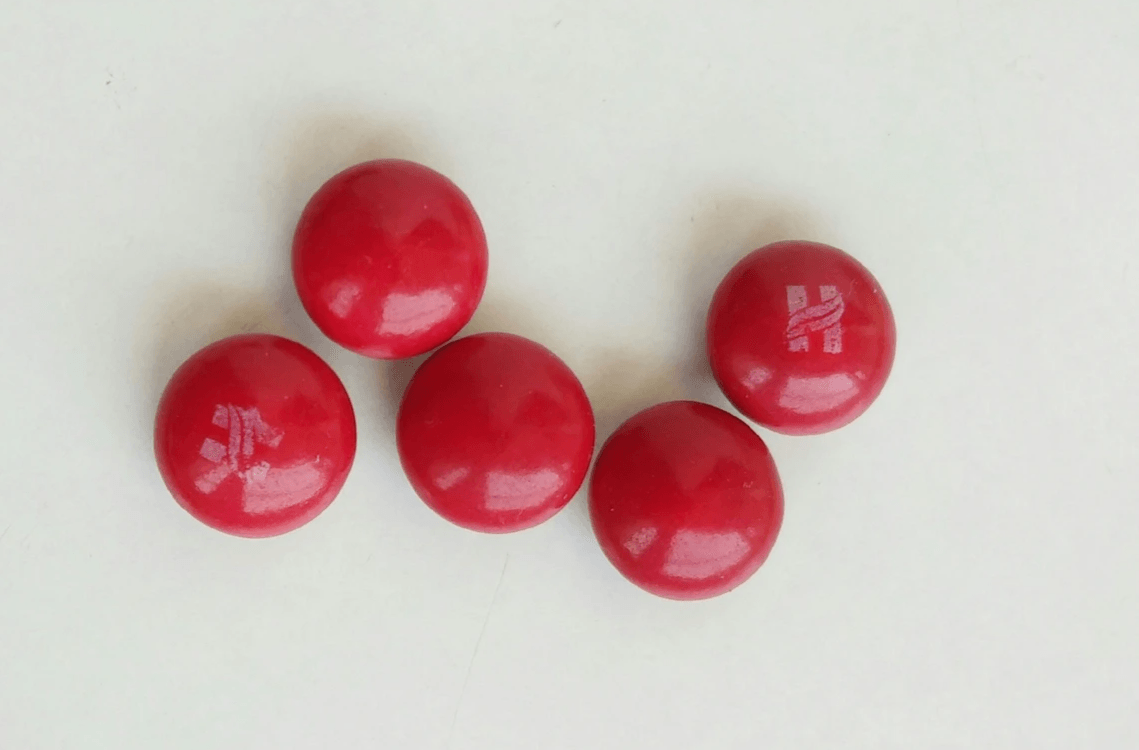
Types of Coating Machines
Standard Coating Pan
Used for semi-automated coating processes. These pans are large rotating containers for mixing the coating solution with the tablets.
Suitable for small-scale manufacturing or traditional processes.
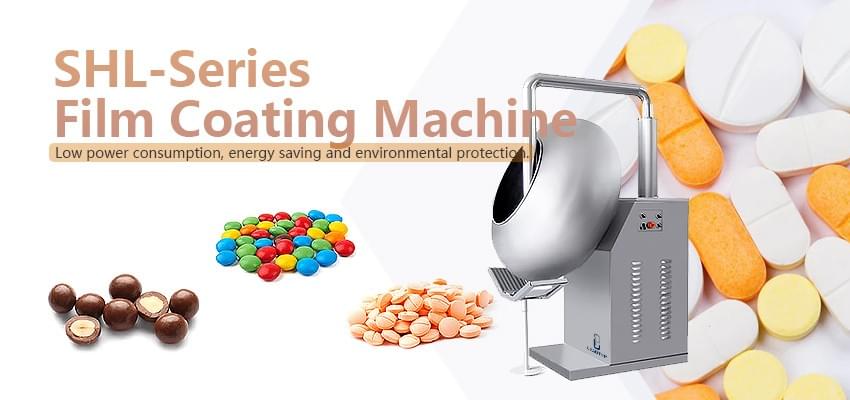
Perforated Coating Machine
Modern coating machine have perforated surfaces, allowing better air circulation and drying during the coating process. These pans are typically equipped with automatic spraying systems.
Ideal for large and medium operations where control and efficiency are crucial.
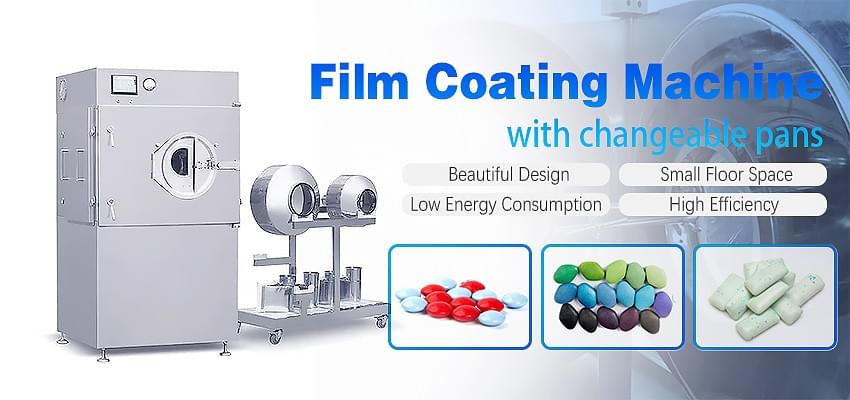
Despite the labor-intensive and complex nature of the sugar coating process, it remains popular for its numerous benefits. Modern advancements have made this process a standard part of tablet production.
Contact Zhejiang Leadtop Pharmaceutical Machinery Co., Ltd (LTPM CHINA) for expert solutions and state-of-the-art sugar coating equipment. For more information, visit our website at osdmachinery.com to explore our extensive range of pharmaceutical machinery.