Tablet strip packing machines are essential for efficiently and securely packaging tablets and capsules in the pharmaceutical industry. These machines ensure the precision and safety required for solid dosage forms. In this guide, we will explain the working principles, advantages, and key differences between strip and blister packing.
How Tablet Strip Packing Machines Work
Strip packing machines follow a systematic process to package tablets:
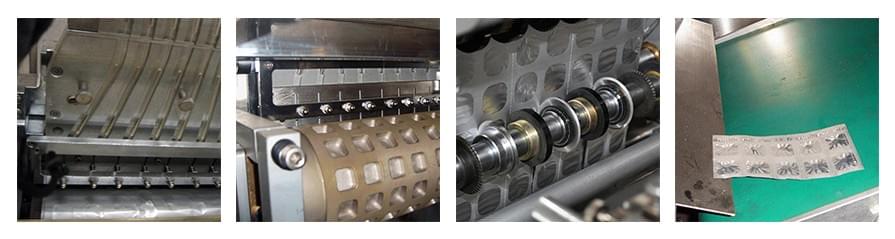
1. Material Loading: Packaging materials like aluminum foil, PVC, or PVDC are fed into the machine. These materials protect the tablets from environmental factors like moisture and light, ensuring product longevity.
2. Filling: Tablets or capsules are placed into pre-formed cavities. Advanced machines ensure accurate filling, using vibration systems to evenly distribute the tablets into each pocket.
3. Sealing: The packaging material is sealed using heat or pressure, creating an airtight and tamper-evident package.
4. Cutting and Coding: Once sealed, the strips are cut to the desired size, and batch numbers are printed for traceability.
Advantages of Strip Packing Machines
1. Accurate Dosing: Each strip contains a fixed dose of medication, minimizing errors and ensuring patient safety.
2. Product Protection: Strip packs provide excellent protection against moisture, light, and air, extending the shelf life of sensitive pharmaceuticals.
3. Tamper-Evident Seals: The sealed packaging offers a strong barrier against tampering, ensuring the medication remains safe until used.
Strip Packing vs. Blister Packing
While both strip and blister packing machines are widely used in the pharmaceutical industry, they serve slightly different purposes:
1. Packaging Method:
Strip Packing: Tablets are sealed between two sheets of material, typically aluminum or PVC, forming continuous strips. This method is ideal for bulk production.
Blister Packing: Tablets are placed in semi-rigid cavities (blisters) formed from plastic or aluminum, and the blisters are sealed with a foil backing.
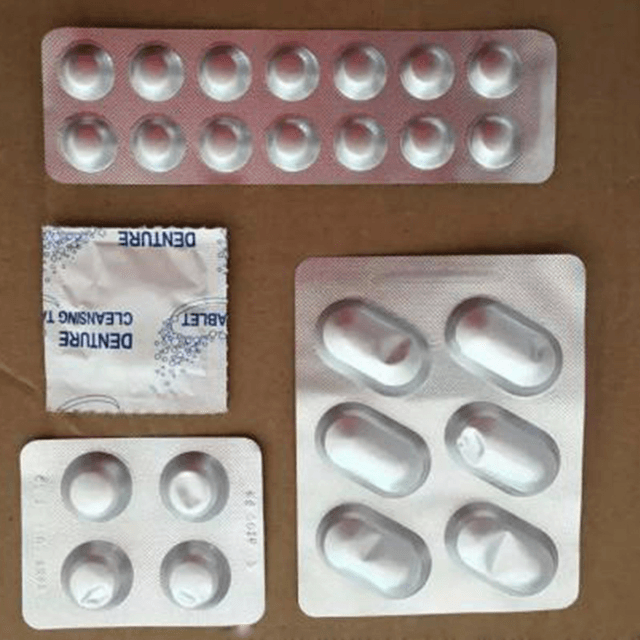
2. Speed and Efficiency:
Strip packing machines often operate at a slower speed compared to blister packing machines, making them more suitable for smaller batches.
Blister packing machines can handle higher output, often favored for large-scale production.
3. Protection:
Strip packing generally provides superior protection against moisture and air due to the use of aluminum-based materials.
Blister packs, while offering good protection, are more vulnerable to environmental factors but allow for product visibility.
4. User Convenience:
Blister packs are often preferred for ease of use, as the tablets are visible and easily accessible.
Strip packs may require tearing, making them slightly less convenient for certain users, such as the elderly or those with limited dexterity.
Applications Across Industries
Pharmaceuticals: The primary application of strip packing machines is the packaging of tablets and capsules, ensuring precise dosing and protection from external conditions.
Nutritional Supplements: Strip packing is also widely used for vitamins and dietary supplements, offering similar protection and convenience.
Tablet strip packing machines play an integral role in the pharmaceutical packaging process by ensuring the accuracy, safety, and efficiency of solid dosage forms. Understanding the differences between strip packing and blister packing can help manufacturers choose the most suitable method based on their specific needs.
For more information on how to choose the right tablet strip packing machine for your production line, feel free to reach out for expert advice!