Tablet and capsule inspection machines play a crucial role in ensuring the quality and safety of pharmaceutical products before they are packaged and distributed. These machines automatically detect defects, such as cracks, discolorations, and shape irregularities, ensuring only high-quality products reach the market. This guide will provide an overview of how these machines work, the different types available, and the features to consider when selecting one for your production line.
How Automatic Tablet and Capsule Inspection Machines Work
Tablet and capsule inspection machines are designed to automatically inspect pharmaceutical products using advanced technology. Here’s a breakdown of the key components and how they function:
1. Hopper and Conveyor System: Tablets or capsules are fed into the machine through a hopper. The conveyor then transports the products toward the inspection area. The conveyor system plays a critical role in ensuring that the tablets or capsules are spread evenly for thorough inspection.
2. Visual Inspection via Cameras: As the tablets move along the conveyor, they pass under high-definition cameras. These cameras are positioned at multiple angles to capture detailed images of each tablet or capsule. The images are processed in real-time using AI algorithms, which detect any imperfections or defects such as cracks, chips, discoloration, or incorrect shape.
3. Defect Detection and Rejection: The system uses predefined parameters to identify defective products. When a defect is detected, the machine activates a pneumatic or mechanical rejection system that removes the flawed product from the production line and directs it to a rejection bin. The accepted tablets or capsules continue on for further processing or packaging.
4. Data and Reporting: Many modern machines are equipped with detailed reporting systems that record inspection data, including the number of rejected products and the nature of defects. These reports help manufacturers improve production processes and ensure compliance with quality standards.
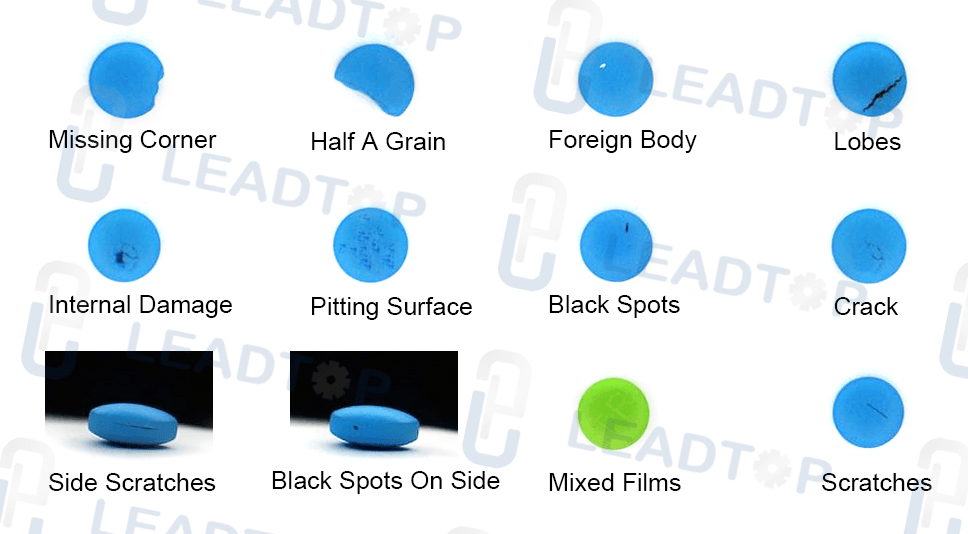
Types of Inspection Machines
There are several types of inspection machines, each designed to cater to different production needs:
1. Visual Inspection Machines: These machines rely on high-resolution cameras to inspect tablets and capsules. They offer reliable inspection for both coated and uncoated tablets and are commonly used in high-speed production lines.
2. AI-Powered Inspection Machines: Advanced machines integrate AI algorithms to enhance defect detection. These systems can learn from previous inspections to improve accuracy over time, making them ideal for manufacturers looking to minimize human error and increase efficiency.
3. Horizontal and Vertical Inspection Machines: Depending on the production setup, manufacturers can choose between horizontal and vertical inspection machines. Horizontal machines are typically more compact and are ideal for small production spaces, while vertical machines are better suited for high-capacity operations.
Key Features to Consider
When choosing a tablet and capsule inspection machine, it’s important to consider several critical features:
1. Speed and Accuracy: High-speed machines can inspect up to 216,000 capsules per hour, making them essential for large-scale production. Accuracy is also crucial, as even minor defects can compromise product quality.
2. AI and Image Processing: Look for machines that use AI-based image processing technology, as this allows for more precise detection of small defects that might be missed by traditional inspection methods.
3. Rejection Mechanism: Pneumatic or mechanical rejection systems ensure that defective products are removed quickly and efficiently without disrupting the production flow.
Automatic tablet and capsule inspection machines are indispensable in ensuring the quality and safety of pharmaceutical products. By using advanced cameras, AI-powered detection systems, and automated rejection mechanisms, these machines enhance product integrity while reducing human error. When selecting an inspection machine, consider factors such as speed, accuracy, AI integration, and the type of rejection system to ensure it meets your specific production needs. Investing in the right equipment will not only improve efficiency but also ensure compliance with regulatory standards, resulting in safer products for consumers.