While automatic bottle labeling machines are designed to make packaging faster and more efficient, they can sometimes run into problems. Understanding common issues and knowing how to troubleshoot them can help prevent production delays and ensure a smooth labeling process. In this article, we’ll explore some of the most common problems with automatic labeling machines and how to fix them.
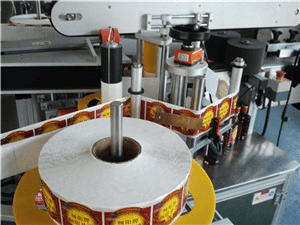
Problem 1: Misalignment of Labels
One of the most frequent issues with automatic labeling machines is misalignment of labels. This can happen if the bottles are not properly positioned or the machine isn’t calibrated correctly.
· Causes:
o Incorrect bottle positioning
o Misaligned conveyor belt
o Damaged or dirty sensors
· Solutions:
o Regularly calibrate the machine to ensure the labels align properly.
o Check that the bottles are placed correctly on the conveyor belt.
o Clean the sensors to remove any debris or residue that may interfere with their function.
Problem 2: Label Jams and Malfunctions
Label jams can occur if the labels are not dispensed correctly or if there is a problem with the machine’s adhesive system. These issues can cause production delays, so it's important to know how to address them quickly.
· Causes:
o Incorrect label roll installation
o Faulty adhesive or sticky residue on rollers
o Poor-quality labels
· Solutions:
o Ensure that label rolls are installed correctly and that they are not damaged or improperly wound.
o Regularly clean the rollers and replace any worn-out parts.
o Use high-quality labels that are compatible with the machine.
Problem 3: Slow Labeling Speed
If the machine is labeling slower than expected, it can affect production timelines, especially for high-volume manufacturers.
· Causes:
o Machine settings are too slow
o Bottleneck in the production line
· Solutions:
o Adjust the speed settings to match production needs.
o Ensure that the entire production line is running efficiently and that the labeling machine is not the cause of the bottleneck.
Problem 4: Inconsistent Label Quality
Inconsistent label quality can affect both the aesthetic and functional aspects of your product packaging. It can also lead to issues with customer perception, especially in industries like cosmetics and pharmaceuticals.
· Causes:
o Uneven label application
o Low-quality or damaged labels
o Incorrect temperature for shrink sleeves
· Solutions:
o Ensure the machine is calibrated to apply the labels evenly.
o Use high-quality, undamaged labels that are compatible with your machine.
o Check the shrink sleeve labeler’s temperature settings to ensure it is applying the sleeves properly.
Problem 5: Machine Maintenance and Wear-and-Tear
Like any other piece of machinery, automatic labeling machines require regular maintenance to keep them running smoothly. Without proper maintenance, machines may break down or perform poorly.
· Causes:
o Lack of maintenance
o Wearing out of machine parts over time
· Solutions:
o Develop a regular maintenance schedule to clean, lubricate, and inspect parts.
o Replace worn-out components, such as belts, rollers, and sensors, before they cause problems.
Preventing Issues and Maximizing Efficiency
Automatic labeling machines offer tremendous benefits for manufacturing efficiency, but they can encounter issues that hinder production. By understanding common problems and taking steps to troubleshoot and maintain your equipment, you can ensure that your labeling machine performs at its best. Regular checks and maintenance are key to minimizing downtime and maximizing the efficiency of your production line.