Tablet molding machines are critical in pharmaceutical production, ensuring precise and efficient manufacturing of solid dosage forms like tablets. When selecting the right machine, it’s important to match production needs, material compatibility, and cost efficiency. This guide will explore key factors to help you choose the best tablet molding machine for your operation.
1. Factors to Consider in Machine Selection
Production Capacity
Tablet molding machines come in different capacities, from small-batch single punch machines to large-scale rotary presses.
- Single Punch Machines: Best for small-scale operations or research and development, where output is relatively low. These machines can produce up to 100 tablets per minute and are ideal for handling smaller quantities and multiple formulations.
- Rotary Press Machines: Suitable for large-scale manufacturing, these machines can produce tens of thousands of tablets per hour. Their multi-station design makes them ideal for continuous, high-speed production.
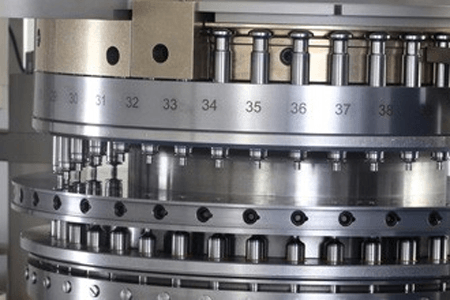
Material Compatibility
Your machine should be compatible with the materials and formulations you're using. The type of excipients (inactive ingredients) and active pharmaceutical ingredients (APIs) can affect tablet consistency and compressibility. Consider the machine’s ability to handle materials that are moisture-sensitive, heat-sensitive, or have specific flow properties.
For heat-sensitive formulations, dry granulation or roller compaction techniques might be more appropriate.
Melt granulation is useful for improving compressibility and flow characteristics of challenging formulations.
2. Automation vs. Manual Control
Manual Control: Suited for small-scale, customized production. Manual machines require more operator input but allow for greater flexibility in tablet customization, making them ideal for research and clinical trials.
Automatic Systems: Fully automated machines offer significant labor savings, reduce error rates, and ensure consistent production. They are especially valuable for large-scale manufacturing where productivity and uniformity are critical.
3. Customization Options
Flexible Tooling: Depending on your production needs, it’s important to select a machine with interchangeable dies and punches. This flexibility allows for producing different tablet shapes, sizes, and thicknesses without needing multiple machines.
Look for machines with B-type and D-type tooling, which support various tablet sizes and ensure high precision in tablet formation.
Modular Design: Machines with a modular setup offer the advantage of easy upgrades and maintenance, which can be cost-effective in the long term. A modular design also allows for adding extra features, such as enhanced safety systems, dust control, or additional feeding mechanisms.
4. Cost-Efficiency and Maintenance
While the upfront cost of a tablet molding machine can be high, it’s crucial to consider long-term cost-efficiency.
Automatic lubrication systems and real-time monitoring can reduce wear and tear, minimizing maintenance costs and prolonging machine life.
Regular preventive maintenance, such as cleaning and calibration, ensures consistent performance and reduces costly downtime.
Also, look for machines that offer remote diagnostics and quick-change tooling, which can drastically reduce downtime during repairs or adjustments.
When selecting a tablet molding machine, consider your production scale, material requirements, and the level of automation you need. Balancing initial costs with long-term productivity and maintenance will help you make an informed decision. For growing businesses, investing in machines with modular designs and scalable capacity ensures the flexibility to expand in the future.