When it comes to pharmaceutical manufacturing, choosing the right coating material for your tablets is essential. Not only does the coating protect the active ingredients, but it also enhances the tablet’s appearance, ensures patient compliance, and can even control the release of the medication. Understanding how these materials work with your coating machine will help you achieve the best results for your production line.
Why Coating Material Matters
Coating plays a significant role in protecting the tablet and making it easier to consume. Different materials serve different purposes:
· Protection: Coatings safeguard tablets from moisture, air, and light, helping to preserve the drug’s potency.
· Taste Masking: Many drugs have bitter flavors. Coatings can cover these, making the tablets more palatable.
· Modified Release: Some coatings control how and where the drug is released in the body, such as delayed-release or enteric-coated tablets that dissolve in the intestines rather than the stomach.
Choosing the right coating ensures that your product remains effective, aesthetically pleasing, and safe for consumption.
Types of Coating Solutions
There are various types of coatings used in the pharmaceutical industry, each with unique features depending on the tablet’s purpose:
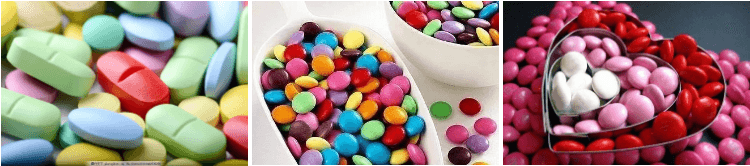
Sugar Coating:
· A traditional method, sugar coating makes the tablets more attractive and masks unpleasant tastes. While it provides a shiny finish, the process is time-consuming and requires multiple layers.
· Best used with: Standard coating pans that rotate slowly, allowing even coating across all tablets.
Film Coating:
· A more modern technique, film coating applies a thin layer of polymer to the tablet. It’s quicker than sugar coating, and the thin layer adds minimal weight to the tablet, making it a popular choice for both taste masking and functional coatings.
· Best used with: Perforated pan systems or fluidized bed coaters, which ensure even and fast drying of the coating.
Enteric Coating:
· Enteric coatings are designed to prevent tablets from dissolving in the stomach, protecting the drug from the stomach’s acidic environment. These coatings allow the tablet to pass into the intestines before releasing the active ingredient.·
· Best used with: Perforated pans or fluidized bed systems for precise application and quick drying.
Factors to Consider When Choosing Coating Materials
When deciding on the right coating material, consider the following:
· Machine Compatibility: Some materials are thicker and require more drying time, while others are thinner and dry quickly. Standard pans are ideal for sugar coatings, while more advanced machines like fluidized bed coaters are needed for thinner film or enteric coatings.
· Desired Properties: What do you need from your coating? For taste masking, you may want a thin film, but if you need to delay the release of the medication, an enteric coating is better suited.
Uniformity and Thickness: If you need a controlled-release tablet, uniform coating thickness is critical. Film coatings generally provide a more uniform layer compared to traditional sugar coatings.
How Coating Materials Impact Machine Performance
The choice of coating material can directly influence how efficiently your machine operates:
Spray Systems: Thicker solutions, like those used in sugar coatings, require slower spray speeds. In contrast, thinner film coatings allow for faster application. Machines with precision spray nozzles will provide better control over coating thickness and quality.
Drying Time: Materials with higher moisture content, such as sugar coatings, take longer to dry. Fluidized bed coaters can speed up this process by improving airflow and providing even drying.
Energy Efficiency: Machines like perforated pans or fluidized bed coaters optimize drying time, making them more energy-efficient, especially for faster-drying coatings like film or enteric coatings.
New Developments in Coating Materials
As sustainability becomes a priority, there’s a shift toward developing eco-friendly coating materials. These new coatings are biodegradable, reducing environmental impact while maintaining their protective and functional properties. Additionally, coatings that improve the ease of swallowing are becoming more popular, enhancing patient compliance.
Selecting the right coating material is key to ensuring your production runs smoothly and your tablets meet the necessary standards. By understanding the relationship between your machine and the coating materials, you can enhance both efficiency and product quality. Whether you're using sugar, film, or enteric coatings, choosing the right equipment and materials is essential for delivering consistent results.
For more information about high-quality tablet coating machines for different production needs, please contact us. We provide tailor-made solutions to help you achieve the best coating results in your pharmaceutical production.