Bottle labeling machines play a crucial role in automating the process of affixing labels to bottles. These machines are widely used in industries such as food and beverage, cosmetics, pharmaceuticals, and more. In this article, we will explore the operating procedures, common troubleshooting, maintenance tips, and efficiency-enhancing techniques for bottle labeling machines.
Overview of the Bottle Labeling Machine’s Working Principle
A bottle labeling machine is designed to automatically apply labels to bottles with precision. These machines use sensors, motors, and rollers to detect the position of each bottle and apply labels in the correct location. The machine ensures that the label is properly aligned and adhered to the surface of the bottle, and in some models, the process is done in high-speed batches. This automation reduces manual labor, enhances efficiency, and ensures high consistency in labeling.
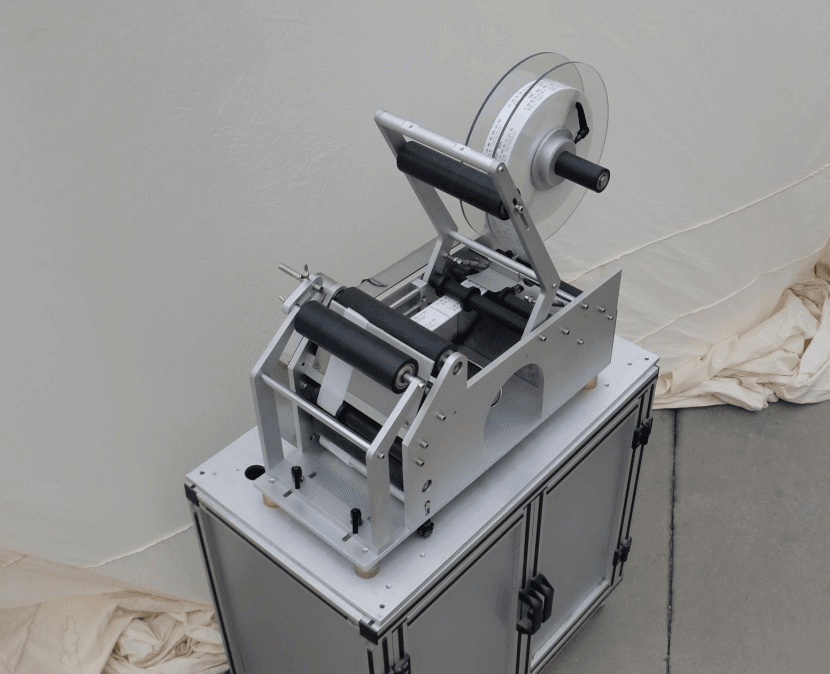
Operating Procedure
1. Preparation Work: Machine Adjustment and Label Settings
Before starting the production process, there are several preparatory steps that need to be followed:
· Machine Setup: Ensure that the bottle labeling machine is placed on a stable and level surface. Check all connections, such as the electrical wiring and air pressure (if applicable). Verify that the machine’s power is connected to a suitable electrical supply.
· Label Adjustment: The size of the label should be set according to the specifications of the bottle being used. Adjust the width and length of the label according to the design and size of the bottles. Make sure the labels are loaded correctly onto the labeling mechanism.
· Bottle Orientation and Positioning: Adjust the guide rails or bottle holders to align the bottles correctly. This ensures that each bottle moves through the labeling machine in the proper orientation.
· Testing the Setup: Run a few test bottles to check if the labels are applied correctly. Ensure the bottles are positioned properly, and labels are aligned without any misapplication.
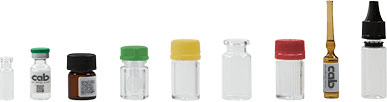
2. Production Process: Automatic Label Application
Once the preparation is complete, the labeling machine moves into the automatic labeling stage:
· Bottle Detection: Sensors or photoelectric devices detect the position of the bottles as they move down the conveyor system.
· Label Application: Once the bottle is detected, the machine applies the label to the bottle using a roller or applicator. The machine ensures that the label is aligned perfectly and adheres to the bottle surface.
· Adjustments for Different Bottle Types: The machine may be adjusted for various bottle shapes (round, square, or irregular) and sizes by fine-tuning the guide rails, height settings, and label feed mechanisms.
· Speed Control: The machine’s speed can be adjusted to suit production needs. Higher speeds can be achieved for large-scale production, while slower speeds may be preferred for small batches or complex labeling designs.
3. Common Troubleshooting and Solutions
In any machine operation, occasional issues may arise. Here are some common problems you might encounter and solutions to fix them:
· Label Application Failure: If labels are not applying correctly, it could be due to an issue with the label sensor or the adhesive roller. Check for any debris on the sensors or the roller and clean them. Additionally, ensure the label is loaded correctly and the feed mechanism is functioning properly.
· Misalignment of Labels: If labels are not aligned properly, adjust the label feed system, rollers, or sensors to ensure proper alignment. Check if the bottles are correctly positioned on the conveyor system.
· Bottles Not Aligning Properly: If the bottles do not align correctly with the labeling mechanism, you may need to adjust the bottle holder or guide rails. Ensure the conveyor speed is consistent and smooth.
· Machine Jams or Stops: Machine jams can occur if bottles are not fed properly or if there’s an issue with the motor or sensor. Check the conveyor system and ensure that there is no debris blocking the path. If the motor is malfunctioning, it may require a professional check-up.
Daily Maintenance Tips
Proper maintenance ensures the longevity of the bottle labeling machine and consistent production. Below are some essential maintenance steps:
1. Cleaning and Lubrication
· Cleaning the Components: Regularly clean the labeling machine to prevent dust, label adhesive, and debris from interfering with the operation. Use a soft cloth and non-abrasive cleaner for cleaning the rollers, sensors, and conveyor belts.
· Lubricating Moving Parts: Lubricate mechanical components such as motors, gears, and rollers regularly to ensure smooth movement. Use appropriate lubricants to avoid wear and tear of these parts.
2. Label Replacement and Mechanical Adjustment
· Label Roll Replacement: Keep an eye on the label roll and replace it when it is close to finishing. Use high-quality labels that match the size and type specified by the manufacturer.
· Adjusting the Mechanical Parts: Over time, the mechanical parts, such as rollers and guides, may wear down. Regularly check and adjust these parts to prevent any misalignment or incorrect label application.
3. Regular Inspection of the Drive System
The drive system (motors, belts, and gears) should be checked regularly to ensure there is no undue wear. Tighten or replace parts if necessary. This helps prevent malfunctions and ensures that the machine operates at optimal speed.
Efficiency-Boosting Tips for Optimizing the Labeling Process
Maximizing the performance of a bottle labeling machine involves several techniques:
· Consistent Bottle Alignment: Ensuring that bottles are consistently aligned on the conveyor reduces the chances of labels being applied incorrectly. Proper guide rails and bottle positioning can make a significant difference.
· Label Roll and Speed Optimization: The labeling speed should be adjusted according to the production volume. Higher speeds are more efficient but can lead to errors, so it’s important to find a balance that works well with your operation.
· Preventive Maintenance: Regular maintenance and early identification of minor issues before they become major problems can help avoid costly downtime and delays.
Common Problems and Answers
Here are some of the most common issues encountered with bottle labeling machines and how to address them:
1. Why are labels not sticking properly to the bottle?
· Possible Cause: The adhesive roller is dirty or malfunctioning.
· Solution: Clean the roller and check for proper adhesive flow. Ensure the labels are in good condition and correctly loaded.
2. Why are labels not aligning with the bottle correctly?
· Possible Cause: Incorrect positioning of bottles on the conveyor.
· Solution: Adjust the guide rails and bottle holders to ensure proper alignment.
3. Why are bottles getting stuck in the machine?
· Possible Cause: A mechanical jam or obstruction.
· Solution: Check the conveyor system for any debris or blockages, and ensure that the motor and gears are functioning properly.
4. Why does the machine stop working or experience frequent pauses?
· Possible Cause: An issue with the electrical system or a faulty sensor.
· Solution: Check the electrical connections, fuses, and sensors for any malfunction.
5. Why is the labeling process slower than expected?
· Possible Cause: Incorrect speed settings or a clogged label feed.
· Solution: Adjust the speed settings and check the label feed mechanism for obstructions.
Proper operation and maintenance of a bottle labeling machine are critical to ensuring high-quality labeling and smooth production processes. By understanding the machine’s working principle, following correct procedures for setup and labeling, troubleshooting common issues, and regularly maintaining the machine, manufacturers can significantly improve operational efficiency and minimize downtime.
If you're looking for a high-performance bottle labeling machine or need assistance with optimization, feel free to inquire. We offer customized solutions and competitive prices to help enhance your production line.