In the packaging industry, particularly for pharmaceuticals, thermoforming and cold forming are two essential methods used to create blister packs. Understanding the difference between these two processes is crucial for choosing the right packaging method for your product.
Thermoforming uses heat to mold plastic, while cold forming uses pressure to shape foil without heat.
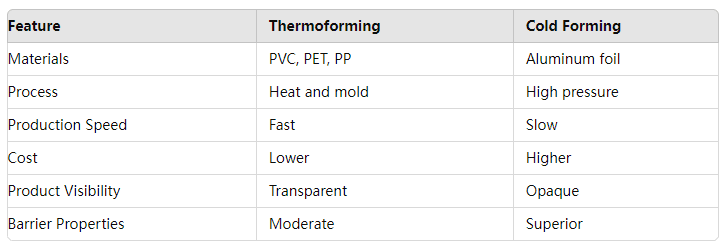
Thermoforming
Thermoforming involves heating a plastic sheet until it becomes pliable, then molding it into a specific shape using a mold. Once shaped, the plastic is cooled and trimmed to create the final packaging.
Key Features:
- Materials Used: Typically, PVC, PET, or PP.
- Process: Involves heating and forming.
- Applications: Widely used for packaging solid pharmaceuticals like tablets and capsules.
- Advantages:
- Faster production rates.
- Cost-effective for high-volume production.
- Transparent packaging for product visibility.
- Disadvantages:
- Less protection against moisture and oxygen compared to cold forming.
Cold Forming
Cold forming, on the other hand, uses aluminum-based laminates. The process involves pressing the material into shape using high pressure, without the need for heat. This method provides a more robust barrier against external elements.
Key Features:
- Materials Used: Aluminum foil, often laminated with plastic and other layers.
- Process: Involves high-pressure molding.
- Applications: Ideal for packaging moisture and light-sensitive products.
- Advantages:
- Superior protection against moisture, oxygen, and light.
- Longer shelf life for products.
- Disadvantages:
- Slower production process.
- Higher cost compared to thermoforming.
- Opaque packaging hides the product from view.
Choosing between thermoforming and cold forming depends on several factors, including the sensitivity of your product, required shelf life, and production volume. Understanding these factors will help you make an informed decision.
Related Topics and Answers:
How to Maintain Your Blister Packaging Machine
- Regular maintenance is crucial for both thermoforming and cold forming machines to ensure efficient operation and product quality. This involves routine checks, cleaning, and timely replacement of worn-out parts.
Common Issues and Troubleshooting
- Thermoforming issues often involve temperature control, while cold forming issues may relate to pressure settings. Proper troubleshooting can prevent downtime and ensure continuous production.
Upgrading Your Blister Packaging Equipment
- Upgrading to newer models can improve efficiency, reduce waste, and enhance packaging quality. Consider features like automated controls and better material handling capabilities.
Comparing Manual vs. Automatic Machines
- Automatic machines offer higher efficiency and consistency, suitable for large-scale production. Manual machines are more suited for small-scale operations or specialized applications.
Tips for Maximizing Efficiency in Blister Packaging
- Optimize material usage, maintain machinery properly, and train operators effectively to maximize efficiency in blister packaging operations.
Understanding the differences between thermoforming and cold forming is essential for selecting the right packaging method for your products. Thermoforming offers speed and transparency, while cold forming provides superior protection. Evaluate your product's needs and production requirements to make the best choice.
For more information on selecting the best blister packaging method for your needs, contact us for expert advice and exclusive offers!