What is Thermoforming Blister Packaging?
Thermoforming blister packaging is a process where a plastic sheet is heated and then molded into specific shapes to form pockets or "blisters" that hold products securely. This type of packaging is widely used for things like medicines, electronics, and small consumer goods. In blister packs, the product sits in the plastic pocket, which is often sealed with a backing made from paper, foil, or another material.
Common materials used in thermoforming include PVC (Polyvinyl Chloride), PET (Polyethylene Terephthalate), and aluminum foil. These materials are chosen because they are strong, clear, and can be easily shaped into the right form for different products.
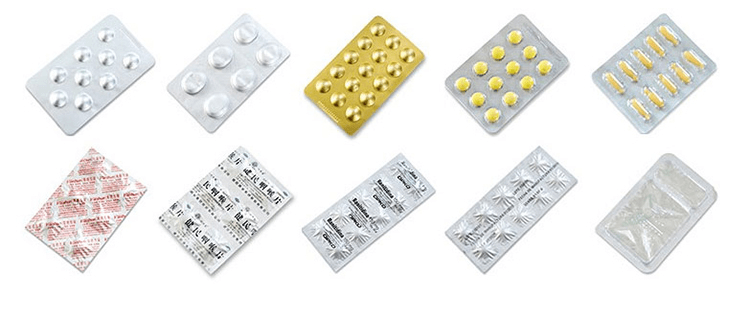
How Thermoforming Blister Packaging Machines Work
Thermoforming machines follow a few simple steps to create blister packaging:
1. Heating: A sheet of plastic is heated until it becomes soft and flexible.
2. Forming: The soft plastic is then pressed or vacuumed over a mold to create cavities or blisters that match the shape of the product. These blisters act as protective pockets for the items being packaged.
3. Sealing: After the product is placed into the blister, the machine seals the blister with a backing, such as foil or paper. This step locks the product securely in the package, protecting it from damage or contamination.
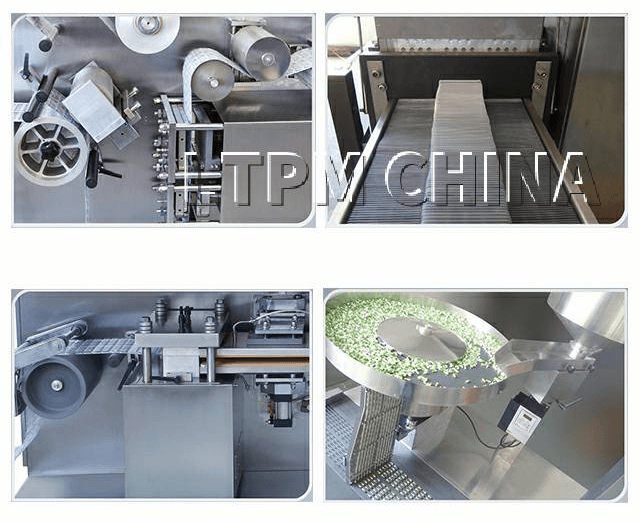
Types of Thermoforming Packaging Machines
There are two main types of thermoforming machines:
1. Inline Thermoforming Machines: These machines are designed for high-speed production and are perfect for factories that need to produce large quantities quickly.
2. Rotary Thermoforming Machines: These machines work in a circular motion and are more suited for products that need special attention in shaping and sealing.
Benefits of Thermoforming Blister Packaging
1. Product Protection: Thermoforming creates strong packaging that keeps products safe from dirt, moisture, and tampering.
2. Customizable: These machines can make blister packs in different shapes and sizes, making them useful for various industries.
3. Cost-Effective: For companies that need to produce large amounts of packaging, thermoforming is fast and relatively inexpensive.
4. Clear Display: Since the plastic used is clear, consumers can easily see the product inside, and manufacturers can add branding and labels to the backing.