Vibrating fluidized bed is a conventional equipment for drying in pharmaceutical industry, which belongs to the type of convective drying. The working mechanism of the convective dryer is that the heat is directly transferred to the wet materials by hot air in the form of convection, and the water vapor is taken away at the same time when the moisture vaporizes. Besides the dryer itself, the device also has fan, heater, separator and other auxiliary equipment. The vibrating fluidized bed is suitable for crystallized particles with particle size more than 100 mesh.
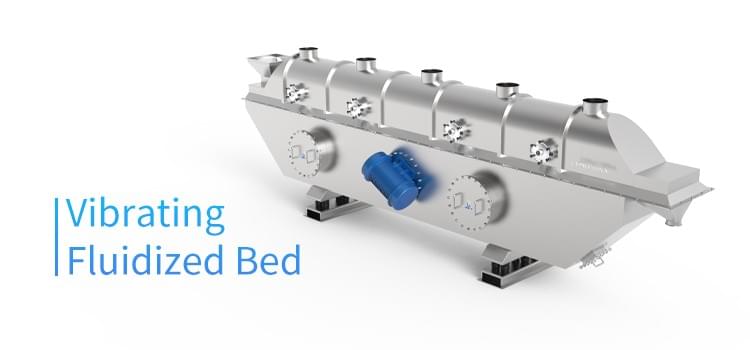
The advantages of vibrating fluidized bed are as follows:
(1) The heat and mass transfer coefficient of the two phases is higher than that of the fixed bed, which can shorten the time and improve the production capacity of the equipment;
(2) The equipment has high production intensity and can be operated continuously or intermittently;
(3) The fluidization of solid particles has the characteristics of fluid, so it is easy to operate and control, and can reduce certain labor intensity;
(4) The equipment is simple and easy to maintain and manufacture;
(5) Good operation safety.
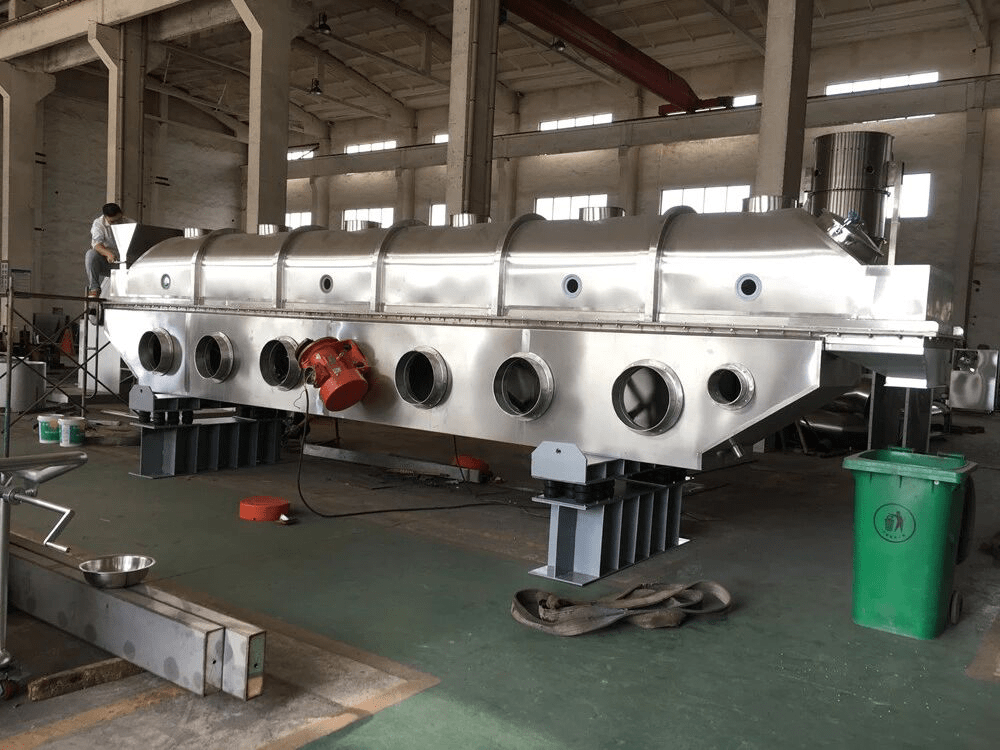
Vibrating fluidized bed also has its disadvantages:
(1) Generally, it is not suitable for materials easy to stick to the wall and agglomerate;
(2) The fluidized bed is not suitable for the fluidization of several materials with different density;
(3) It is not suitable for materials with strict requirements on product shape;
(4) There are certain requirements for the particle size of the material during the operation of the Vibrating fluidized bed, and the particle diameter is generally 30 μ m ~ 6 mm. If the particle size is too small, it is easy to be carried away by air flow, and too large is not easy to fluidize;
(5) Due to the need for fans, heaters, separators or dust catchers and other ancillary equipment, the equipment is bulky and covers a large area;
(6) It has the advantages of low heat loss and high thermal efficiency (generally up to about 80%). The thermal efficiency of vibrating fluidized bed is generally 40% - 60%. From the point of view of energy saving, it is necessary to improve the thermal efficiency.
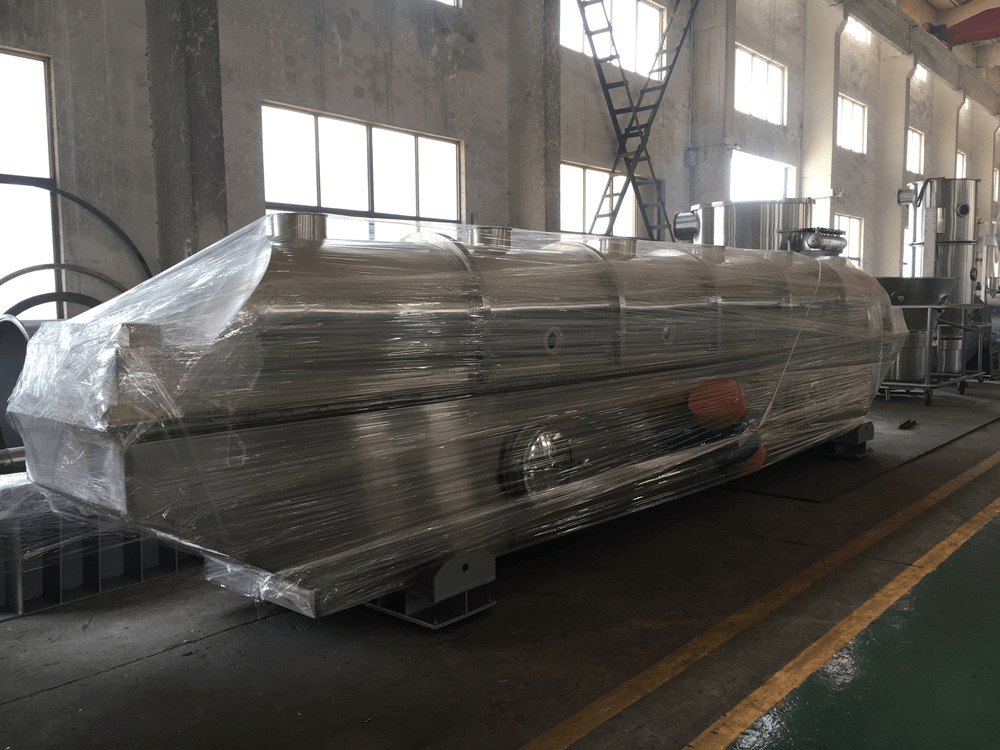
Vibration fluidized bed equipment is widely used in pharmaceutical, chemical, food and other industries because of its simple structure, easy maintenance and good safety. At present, the common types of fluidized bed drying equipment in pharmaceutical industry mainly include boiling dryer, horizontal boiling dryer and vibrating fluidized bed dryer.
As far as fluidized bed equipment is concerned, its defect is first of all low energy utilization rate, belonging to high energy consumption equipment. The energy consumption of vibrating fluidized bed is mainly the electricity consumed by fans and the steam consumed by heater heat exchange. Steam consumption accounts for a large proportion of energy consumption. For the design and manufacturers of vibro fluidized bed, it is necessary to improve the energy utilization rate of vibration fluidized bed in terms of technical measures.
On the basis of summing up the application practice, I think there are three ways to improve the energy saving effect:
(1) Strengthen the sealing effect of vibrating fluidized bed. In the past, the boiling pot of some boiling dryers was not well combined with the equipment body, and there was serious air leakage phenomenon. In this way, the outside cold air entered the pot, greatly reducing the temperature of hot air, affecting the drying effect and reducing the thermal efficiency;
(2) Improve the heat exchange effect of heater. The heater is rough in construction and has low heat exchange efficiency, which will increase steam consumption. At present, many dryers equipped with fluidized bed drying equipment use steel tube wound fins for heat exchange. Although steel pipe can save material cost, it is not as good as copper tube in heat transfer;
(3) Reuse the exhaust air. When the temperature of the tail air extracted from the fluidized bed is higher than that of the natural air, a part of the tail air can be used to enter the heater to reduce the steam loss.
In addition, each type of drying equipment has its own advantages, and the combination of various types of drying equipment is also one of the ways to save energy. In order to save power consumption, fluidization drying is adopted in the early stage of drying, and microwave drying is used in the later stage of drying, which shortens the drying time and saves the steam consumption.